Add your feed to SetSticker.com! Promote your sites and attract more customers. It costs only 100 EUROS per YEAR.
Pleasant surprises on every page! Discover new articles, displayed randomly throughout the site. Interesting content, always a click away
Alene Candles in the news
Alene Candles is a full-service contract and private-label manufacturer of superior custom-designed filled candles for the gift, cosmetic and retail markets. Its industry expertise has allowed it to produce for some of the world’s best-known brands. The company prides itself in exceeding quality and delivery expectations, and in its ability to customize solutions across a range of candle and home-fragrance productsReal Learning, Artificial Intelligence 6 Dec 2024, 6:08 pm
Alene internship offers opportunities for creativity and growth for both company and local college student
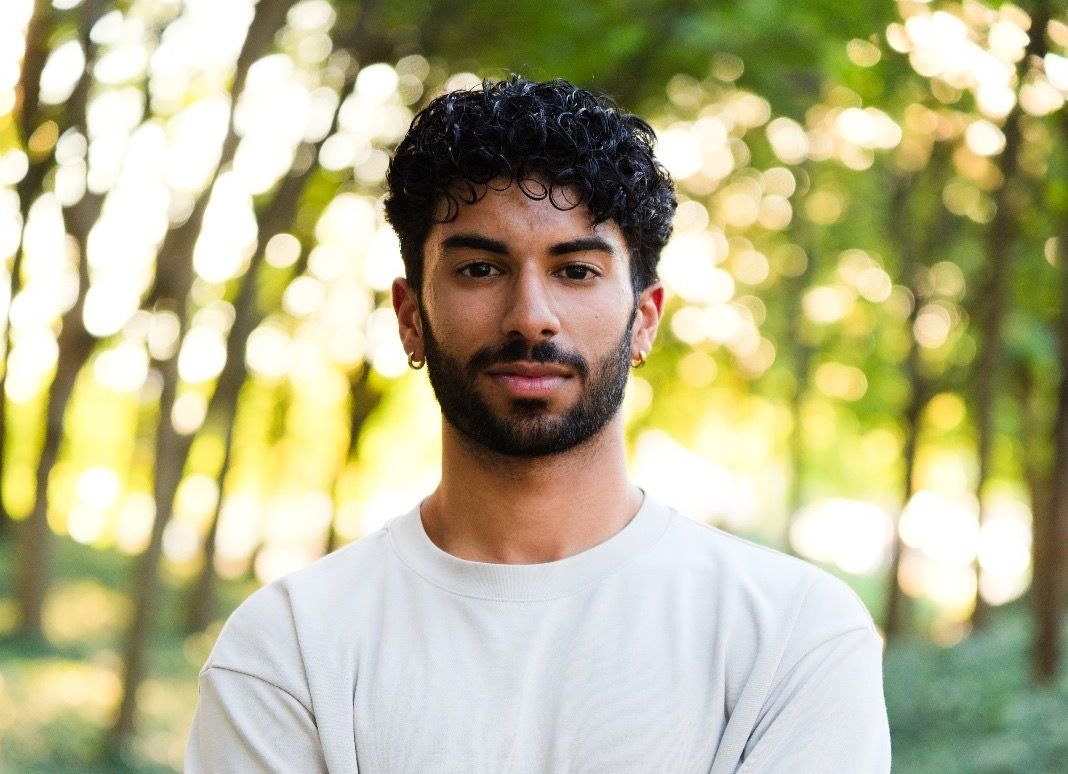
Ohio State University junior Sagar is studying computer science and neuroscience, with the intent of understanding how the two intersect to create artificial intelligence (AI). The country’s largest contract candle manufacturer might seem like an odd fit for that skillset, but as it turns out, Sagar and Alene Candles are a perfect match.
At Alene, all employees are encouraged to suggest ways AI can be incorporated into their jobs to help the company innovate. This year, Alene created a summer internship position to help turn some of those ideas into reality.
“When I came in, I started helping with the generative chat, especially on the back end,” says Sagar of the in-house chatbot that Alene Candles has been building. The chatbot is one of the many AI pilot programs Application Developer Daniel M. and his team are working on.
“Whether that's retrieving documents in a way that makes them easier for a human to understand or being able to ask questions about procedures or step-by-step guides, the first thing we were looking to solve was how we can get some of these documents into an AI chatbot so we can interact with them,” says Daniel. “[Employees can] ask thoughtful questions and get thoughtful responses and even images back from those documents,” with all the information being specific to Alene’s machines and procedures.
AI in manufacturing often centers on a subset called machine learning, or ML. Programming machines to interpret production data helps optimize the production process and better predict and prevent machine failure. AI is also used by some companies to improve efficiency in the supply chain and enhance product design.
Sagar, who has expanded his internship into a part-time role, is now working on a project using machine learning and computer vision—another subset of AI where computers analyze visual data—to understand whether these technologies are useful in other areas of the business.
“Our manager has given us a lot of freedom to explore, which I think is another really important aspect of this—not just handing over assignments, but letting us explore, see different possibilities and then bringing those to the table and saying, ‘this is what we could implement,” said Sagar.
For Sagar, this experience is a dual opportunity—applying fundamental concepts he learns in school while bringing that real-world experience back to the classroom.
“Anytime you get hands-on experience it’s a lot different from school. I think it's been a great opportunity as a whole.”
Alene Candles Names New Chief Financial Officer 26 Apr 2024, 6:25 pm
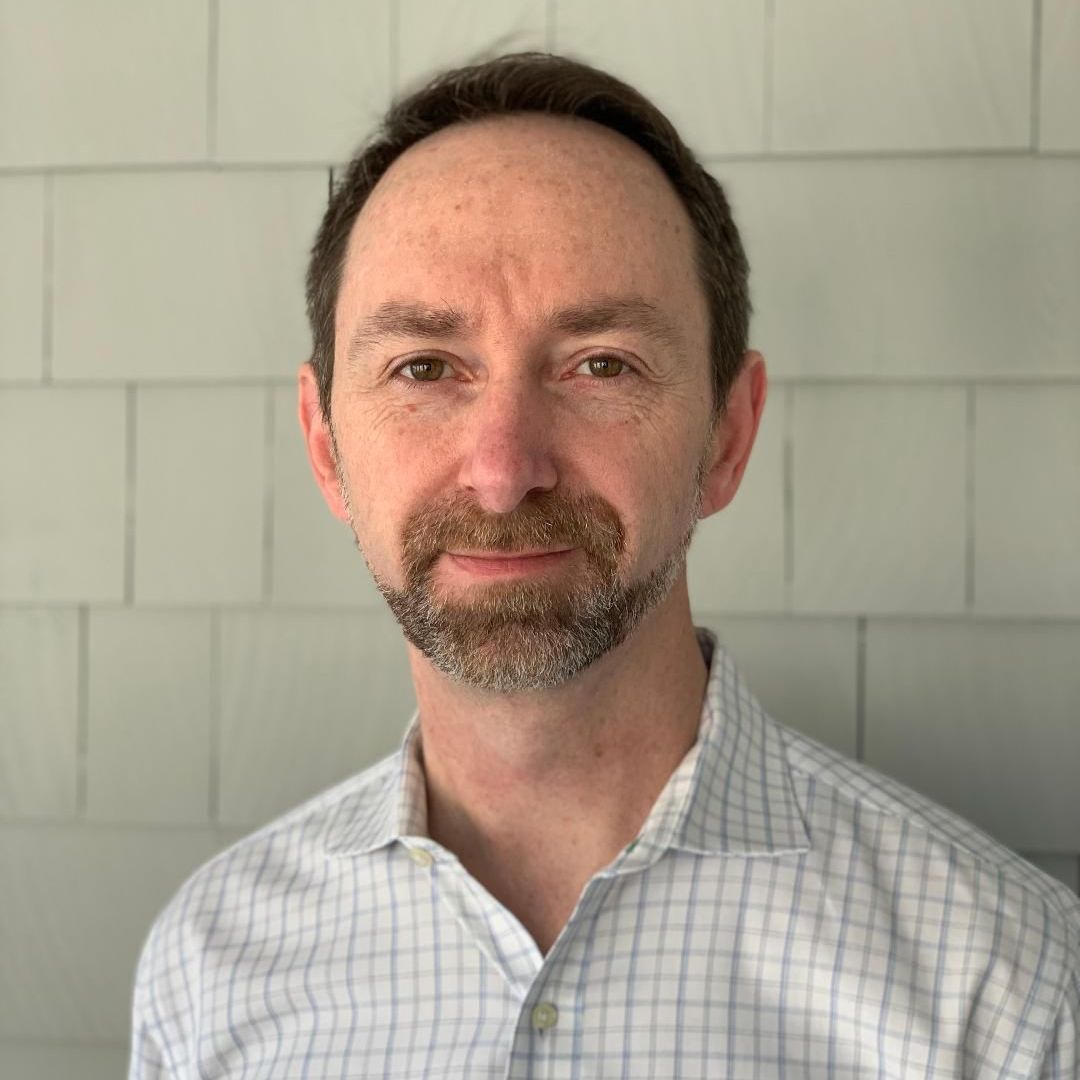
Alene Candles, the nation’s leading manufacturer of contract, private-label home fragrance products, welcomes Bill McDonald as the company’s new Chief Financial Officer. McDonald comes to Alene with a strong background in corporate fiscal management, strategic planning, and business growth. Previously, he was CFO at Wellness Pet, LLC, where he helped lead the company through a period of significant expansion.
“Bill brings tremendous experience and a proven track record in driving business growth and working with people. He is a wonderful addition to the Alene team,” said Alene Candles President & CEO Raj Chary.
Bill is a graduate of Stonehill College and a member of the American Institute of Certified Public Accountants.
“Alene is a great company where quality people make quality products,” said McDonald. “I’m grateful for the opportunity to be a part of its exciting future and am looking forward to working with the teams in New Hampshire and Ohio.”
Alene Candles’ Rod Harl Recognized by NH Business Review 12 Apr 2024, 4:46 pm
Rod Harl Named a Top 200 New Hampshire Business Leader
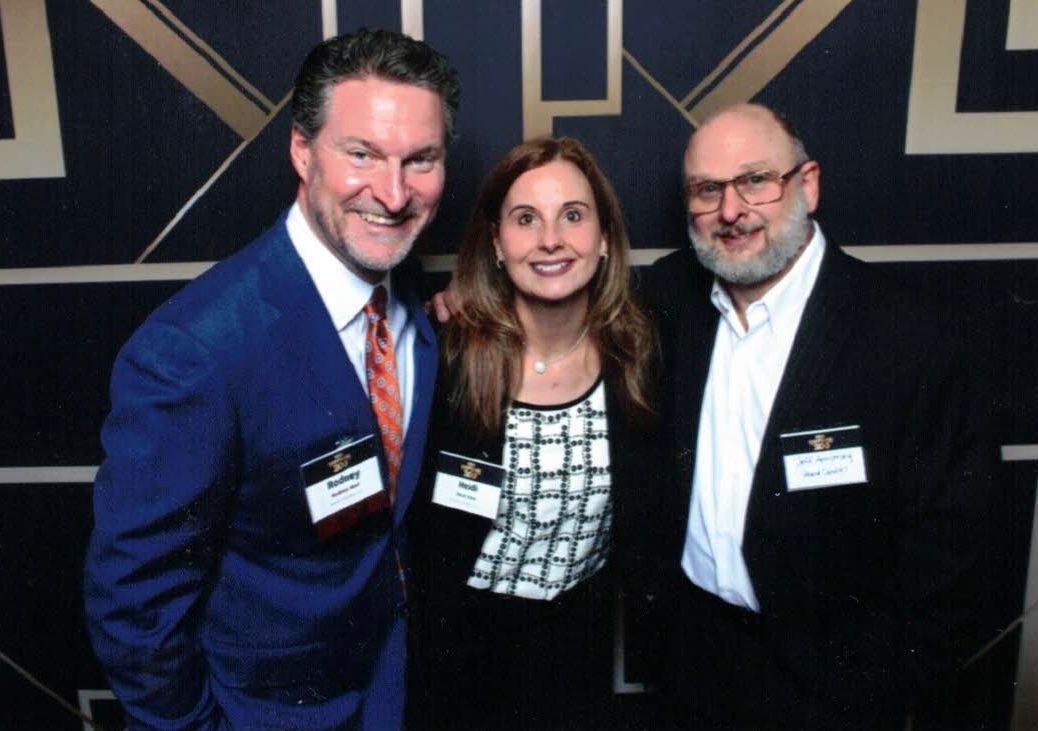
Rod Harl, Chairman of Alene Candles , the nation’s leading full-service contract and private-label candle and home fragrance manufacturer, has been named one of New Hampshire’s 200 top business leaders in 2024 by NH Business Review (NHBR). On Thursday, April 11, Harl was recognized alongside fellow recipients at the New Hampshire 200 reception.
“My success as a business leader in New Hampshire is thanks in large part to our incredible team at Alene,” said Harl. “I am humbled to have been named in the 2024 Top 200 list.
”Alene was founded in 1995 and purchased by Harl and Chief Business Development Officer Ted Goldberg in 2008. Under Harl’s leadership, Alene has enjoyed tremendous growth, with facilities in both New Hampshire and Ohio. He recently transitioned into the role of Chairman, with Raj Chary succeeding him as President & CEO earlier this year
.“Rod has a gift for connecting with people and he’s invested in the personal and professional success of every Alene employee,” said Chary. “This has shaped Alene into the company it is today and made a difference in the communities where our employees work and live.
”Alene employs more than 400 full-time and 500 contract associates annually with operations in Milford, New Hampshire, and two sites in New Albany, Ohio. In addition to providing the highest-quality products to clients using innovative methods, Alene invests in tailored professional development programs available to every employee. The company was recognized as one of Business NH Magazine’s Best Companies to Work For in 2021 and 2022 and won Business NH Magazine’s 2023 Business of the Year award in the manufacturing category. NHBR’s New Hampshire 200 list is published biannually. This year, honorees were nominated by recipients from the 2020 and 2022 classes
Alene Candles Receives Encova Insurance Safety Award 2 Apr 2024, 1:49 pm
The nation’s leading candle and home fragrance manufacturer named a 2023 Encova Insurance Safety Award honoree
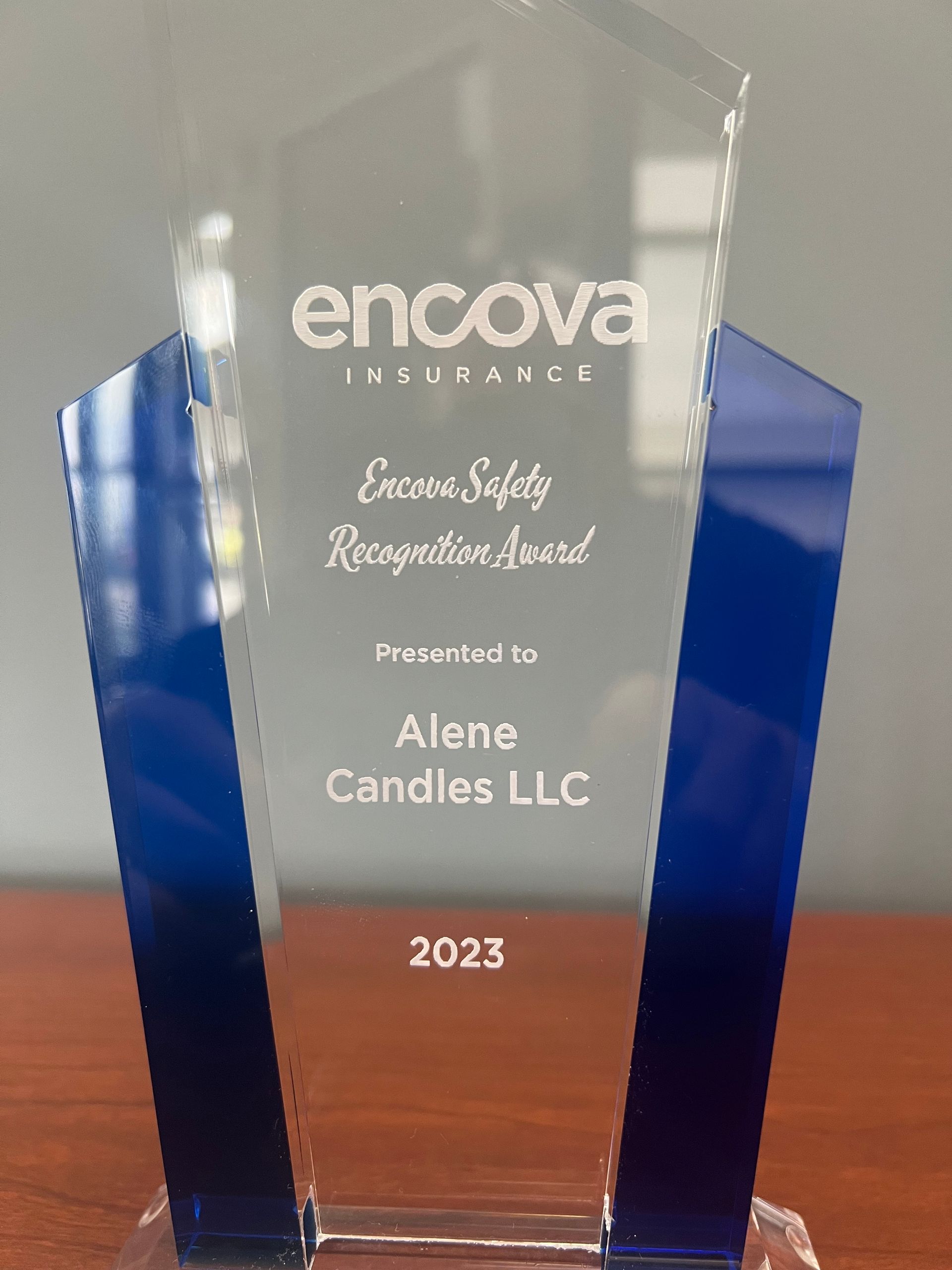
On Tuesday, March 26, Alene Candles, the nation’s leading contract manufacturer of candles and home fragrance products, was recognized by Encova Insurance as a 2023 Safety Award recipient. The award was presented to Phil Erickson, Vice President of Operations, at Alene’s New Albany facility and commends safe operations in both Ohio and Milford, New Hampshire.
“This award reflects the commitment every Alene team member makes to safety, every day as a deeply embedded part of our culture,” said Erickson. “We are proud to be recognized as a leader in the workers’ compensation safety improvements space.”
Encova Insurance has honored policyholders since 2019 for demonstrating success in key safety areas through its Encova Safety Award Recognition Program. Alene Candles was recognized by Encova for its commitment to controlling and reducing losses and exposures, actively working safety and loss control service strategies to achieve measurable elements of the Roadmap to Safety Success, and implementing recommendations to reduce exposure.
Alene employs more than 400 full-time and 500 contract associates annually with operations in Milford, New Hampshire, and two sites in New Albany, Ohio. It was named a Business New Hampshire Magazine 2023 Business of the Year, as well as a 2020 and 2021 Best Companies to Work For.
Alene Candles Announces New President & CEO 4 Mar 2024, 5:39 pm
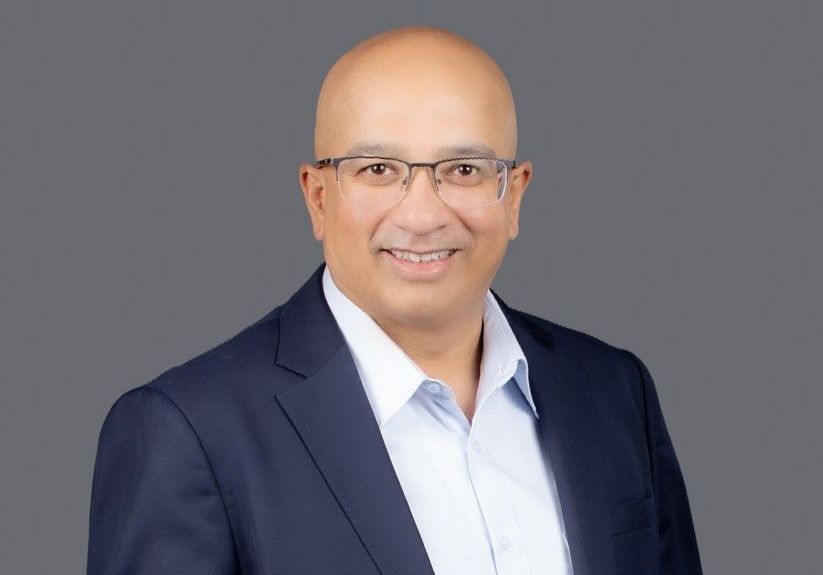
Alene Candles, the nation’s leading contract manufacturer of candles and home fragrance products, has named Raj Chary to the role of President and CEO. Chary brings more than 20 years of experience as a seasoned executive, with expertise in general management, strategy, organizational development, operational improvement, and commercial excellence. Rod Harl, who has led the company since purchasing it with business partner Ted Goldberg in 2008, will transition into the role of Chairman.
“Raj’s diverse professional background and fresh perspective make him an ideal fit to lead Alene into the future,” says Harl. “Ted and I are impressed by his vision and the way he connects with the Alene team. I could not imagine leaving this role in better hands and am excited for what lies ahead for the company and our dedicated employees.”
Chary brings global experience to Alene, with prior leadership roles in Europe and Asia Pacific. He was most recently Vice President at Cabot Corporation, a producer of specialty and performance products, and previously advised Fortune 500 clients while at McKinsey & Company. At Alene, he is looking forward to being a part of the dynamic team and solidifying the company as the leading manufacturer of home fragrance products.
“Both the people and the possibilities at Alene are energizing,” says Chary. “There’s a collective feel that people enjoy working here, which is reflected in their commitment to quality and the tremendous growth and innovation Alene has experienced, especially in recent years.”
Alene employs more than 400 full-time and 500 contract associates annually with operations in Milford, New Hampshire, and two sites in New Albany, Ohio. It was named a Business New Hampshire Magazine 2023 Business of the Year, as well as a 2020 and 2021 Best Companies to Work For.
Alene’s commitment to creating the best products in the world, passionately and profitably, is met by developing innovative solutions to business challenges and by investing in the leadership potential of each full-time employee.
The company’s “Efficient Artisanship” approach sets the standard for American manufacturing by increasing quality and shortening delivery time with on-site research and development, a domestic supply chain, and an industry-leading warehouse and distribution system.
“I’m thrilled to have the opportunity to guide Alene in its next phase of growth, building on the creativity, innovation, and processes that have made this company an industry leader,” says Chary.
Alene Candles Recognized by Business NH Magazine as Top 100 Private Company 22 Dec 2023, 6:23 pm
Alene Candles Again Named a Top 100 NH Private Company
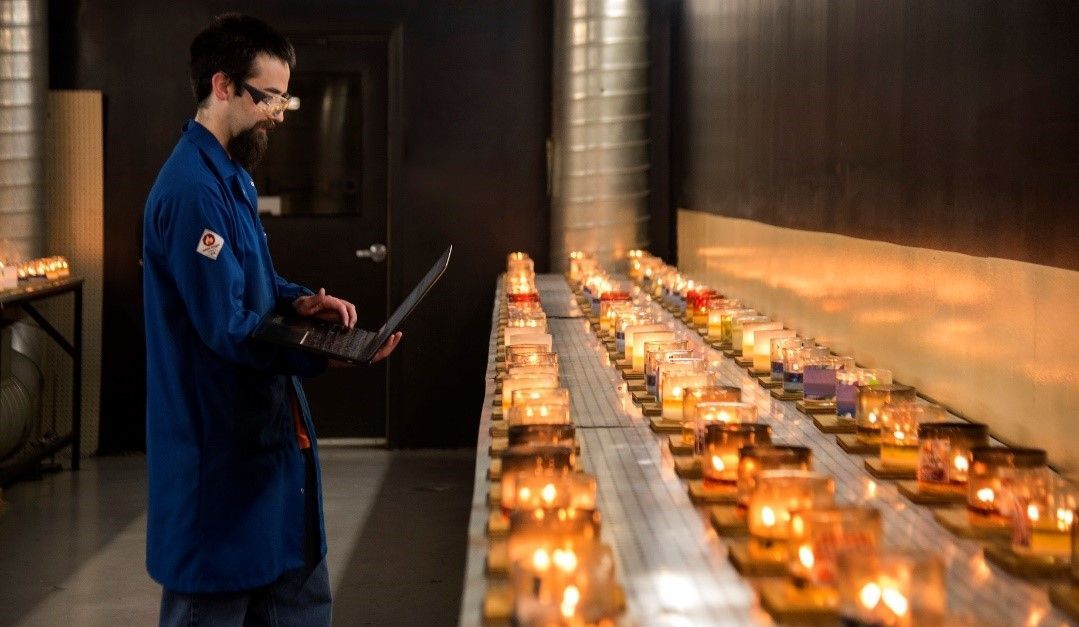
The body content of your post goes here. To edit this text, click on it and delete this default text and start typing your own or paste your own from a different source.
Business of The Year: Alene Candles 21 Dec 2023, 6:14 pm
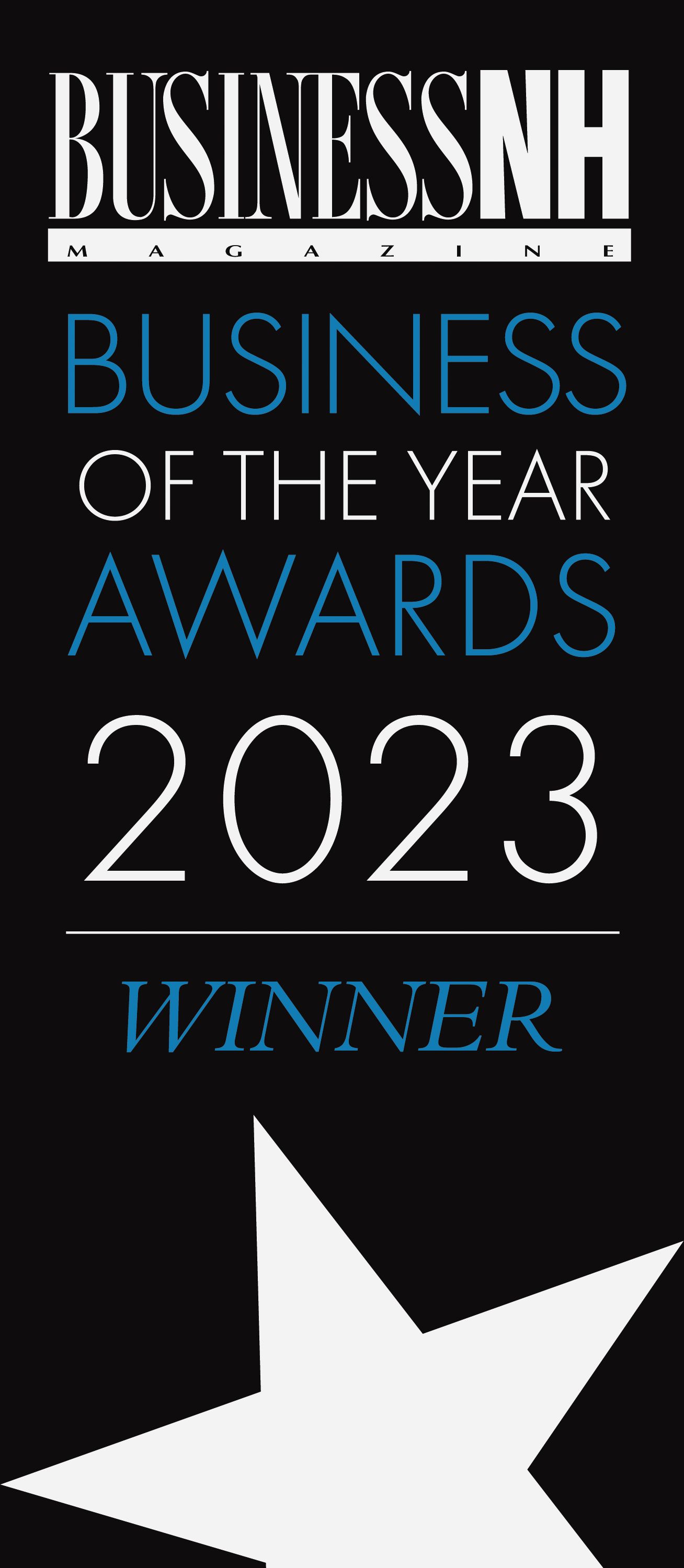
Since President and CEO Rod Harl and Managing Partner Ted Goldberg bought Alene Candles in 2008 from the Amato family, they have dramatically grown the private-label candle manufacturer, adding nearly 300,000 square feet to its facilities in NH and building two facilities in Ohio. Alene Candles can now produce more than one million candles daily across the company and made more than 100 million candles last year.
When the partners bought the company, Alene Candles had 75 employees but now boasts a workforce of 462 with 213 employees in NH. Sales in the first 10 years of Harl & Goldberg’s ownership increased seven-fold and despite the pandemic, sales have continued to grow more than 80% in the last five years.
Innovation has spurred its success. Alene Candles has more than 40 scientists and engineers who have developed new detection methods to identify flaws in raw materials and work with suppliers to correct them. Alene earned a patent for a new way to mass produce marbled candles.
Innovation has spurred its success. Alene Candles has more than 40 scientists and engineers who have developed new detection methods to identify flaws in raw materials and work with suppliers to correct them. Alene earned a patent for a new way to mass produce marbled candles.
“We think of ourselves as a manufacturing services provider who happens to make candles,” Harl says. “It involves making candles, but it may also involve fulfillment, design and technical innovation to meet their needs.”
This is a company that steps up in times of crisis. When the pandemic hit, Alene Candles quickly pivoted and produced more than 60,000 face shields over five weeks for first responders. In December 2021, when a tornado destroyed homes and a competing candle production facility in Kentucky, employees and the company raised $40,000 to help tornado victims.
Alene Candles finds various ways to support its community. Through “Alene Gives Back,” the company pays employees up to eight hours annually to volunteer in the community, including helping at the NH Food Bank or doing community cleanup projects. Over the years, Alene Candles has recognized community members who have made significant contributions to Milford through its Milford Luminaries program, donating $1,000 to a charity of their choice.
For the past eight years, Alene Candles has partnered with the Souhegan Valley Boys and Girls Club to award an annual scholarship to a Milford High School graduate who plans to study science. It is one of three companies that sponsor the Manufacturing Exploration and Externship Program with Milford High School’s Applied Technology Center.
“Our secret sauce is being good to people and doing the right stuff,” Harl says.
Business scents: Alene Candles produces specialty candles at its Milford facility 21 Dec 2023, 5:35 pm
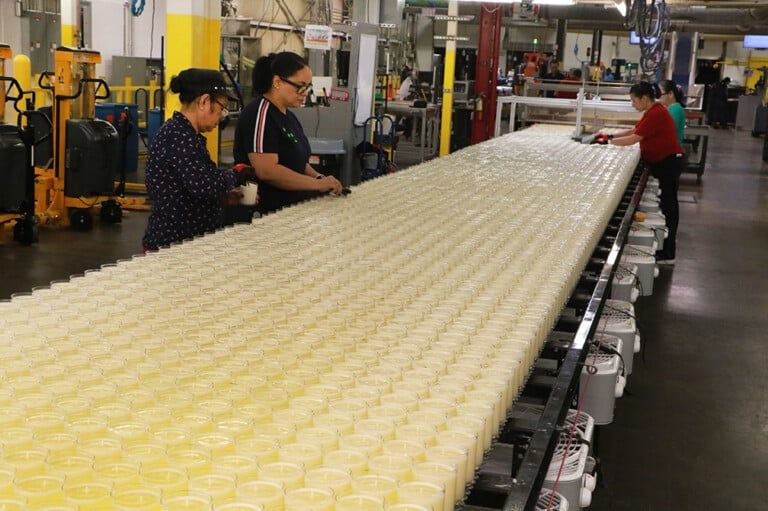
If you bought a candle from a name-brand retailer during the Christmas season, there’s a good chance it was made by Alene Candles, a Milford private-label company that produces more than 100 million candles every year.
Alene, founded in 1995 by Paul and Nancy Amato, was acquired by business partners Rod Harl and Ted Goldberg and a group of investors in 2008. The company opened a second factory in New Albany, Ohio, in 2012 and expanded that facility in 2020. It employs 1,100 people, including 450 in New Hampshire.
Alene has greater capacity at its Ohio factory than it does in New Hampshire, where the cost of labor, energy and housing are high, said Harl, Alene’s president and CEO. The New Hampshire location is also more constrained by geography; it’s expensive to ship materials in and out.
“We can’t do really, truly high-volume manufacturing here in the Northeast. So we do boutique work, and it means we can apply more skill to the product,” he said. “We do our high-volume work in Ohio, and we do our specialty work here.”
In October, Harl led a group from NH Business Review on a tour of the Milford factory, where we learned about the complexities of candle manufacturing, which relies on chemistry, engineering, ingenuity and hard work.
While automation has made candle-making more efficient, workers are needed along the production line to make adjustments, such as making sure wicks are straight after hot wax is poured into glass containers.
We started our tour at Alene’s research and development building, where work on new products begins. While the company specializes in candles, it also produces a line of diffusers, which emit essential oils into the air to aid relaxation.
Alene makes candles housed in glass, pressed glass, metals, ceramics and lead glass, and the candles can weigh anywhere from a couple of ounces to nearly 3 pounds, said Lilia Morales Pruneda, director of research and development and analytical technical services.
“We’re always looking for new products that are available in the market,” Pruneda said. “Most of our waxes are either food grade, pharma grade or cosmetic grade, so you can pretty much fry doughnuts in the waxes that we use.”
Once a new formula is tested, Alene offers it to its customers. Then the sample lab takes over.
“We take the customer’s preferred fragrance, and at the load that they want and the wax that they want, and then we will put it into the glass that they’ve chosen, whether it’s 3-pounder or down to the 2-ounce votives,” said Glenn Perrone, who manages the lab.
All the samples are made by hand.
“I’ve got four technicians on two shifts who will then mix the waxes, mix in the fragrance, and if we have to do colors, they’ll mix the colors and make the colors as well,” he said.
Then the technicians will take the temperature of the candles.
“As they’re cooling, we’ll develop a cooling curve. We’ll pick the wicks and find a wick that works the best for the customer, with the safest flame, because we don’t want any candles burning up anyone’s houses.”
Before the sample candles are presented to the customer, they are tested in Alene’s safety lab.
“There’s a lot of testing going on to make sure that the wicks we choose will not overheat or cause any fracture of the glass or cause anything to burn or go out too soon,” Perrone said.
The company’s engineering team will feed that information into the production line, so workers know how fast to pour the wax, how hot it has to be and how fast to cool it, he said.
“Does it need a second pour? Does it need a second reheat to make the surface nice and smooth?”
How the candle is going to be packed — which might include heavy Styrofoam packaging with a lid — is the final part of the development process, Pruneda said.
“To completely cool the candle, it could take up to 36 hours. So we need to consider that when we are manufacturing,” she said. “When are we going to be packing it? How are we going to pack it?”
In another lab, chemists like Ibrahim Muhic run tests on the fragrances used in the various lines of candles, which feature 3,000 varieties, including 800 new formulations.
“We’re responsible for validating all new fragrance arrivals and making sure that they’re good to use before they move on to the sample and to be used in candles,” Muhic said. “When we receive a new fragrance, we’ll start off by looking at the documentation, the safety data sheets. We’re looking at component composition, physical chemical properties such as flashpoint, any other hazards that we should be aware of.”
Work spaces are smaller and the volume is lower at these stages of the candle manufacturing process than they are on the factory floor. It’s where technicians are making sure ingredients are working as intended before the candles are approved for mass production.
On the production line, Matthew Link, a supervisor for the second shift, monitored a machine that was pouring hot wax into glass jars and sending them down a conveyor belt to waiting workers, ready to inspect them as they made their way toward a packaging station.
While the system is automated, workers make adjustments as needed.
“One of the things that’s big is making sure we hit the right temperatures. So they’re doing their temperature checks all throughout the day,” Link said. “It’s very important that you don’t have a cold wax going into a hot wax.”
The mix of automation and human hands improved efficiency along the production line.
“I can’t say it was a no-brainer. The technology existed, but we did make some improvement to it,” Harl said.
It’s the kind of investment the company is consistently considering as the industry evolves.
“The consumer will only pay so much for a candle, and you start to price yourself out of the market in terms of what’s sensible,” Harl said.
Alene Candles Launches New Americans Welcome Program 21 Nov 2023, 7:43 pm
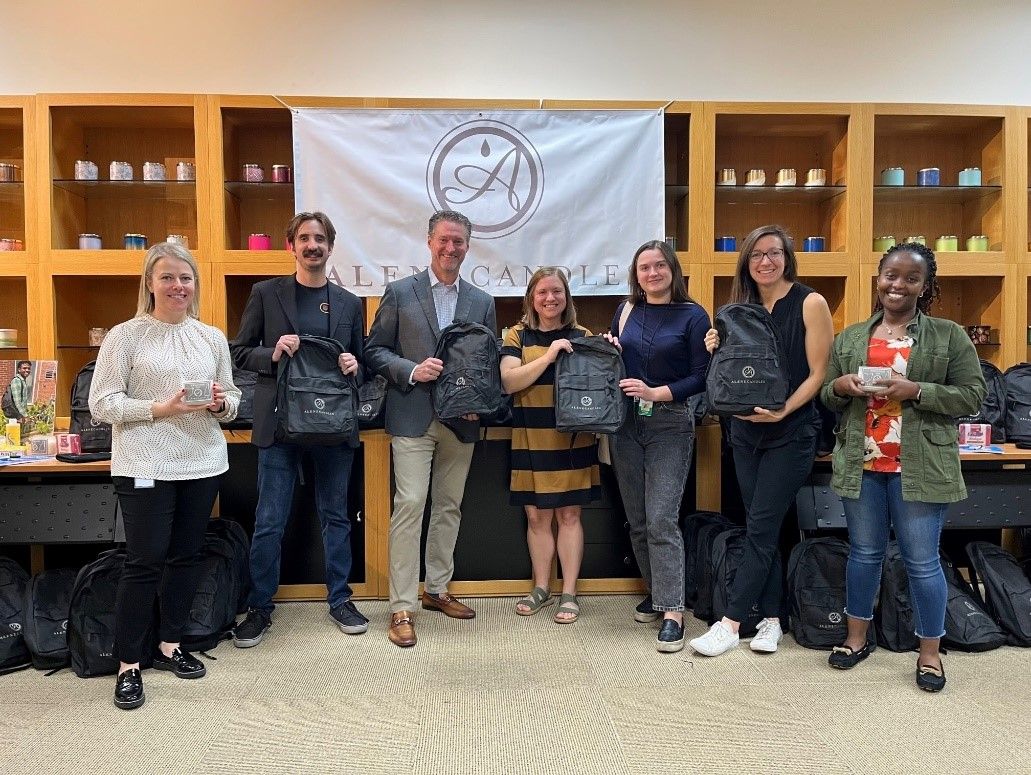
New Albany, OH – Alene Candles , the nation’s leading full-service contract and private-label candle and home fragrance manufacturer, officially launched its New Americans Welcome Program at a kit-assembly event on Tuesday, September 26, at its facility in New Albany.
Alene is partnering with three Columbus-area nonprofits, Creating Central Ohio Futures (CCOHF), Community Refugee & Immigrant Services (CRIS-OH) and Ethiopian Tewahedo Social Services (ETSS), to provide welcome kits to their clients. Included in the kits are several practical and personal care items, an Ohio-themed children’s activity book, and an Alene-made candle, all in a durable backpack for the families to use.
“Central Ohio’s new Americans are a vital part of the region’s tremendous success story,” said Rod Harl, president and CEO of Alene Candles. “These welcome kits are a small gesture that send a big message to the immigrants and refugees in Greater Columbus — Ohio welcomes you, Alene welcomes you, and we appreciate the contributions you make to our workforce and community.”
Alene Candles piloted the program over the summer with 240 kits, all assembled by Alene volunteers. Another 120 kits were packed and distributed on Tuesday, with 270 more to follow in the coming months.
“The majority of the families we serve came to the U.S. with so little — gifts like these certainly bring a smile to weary faces and make a space feel a bit more like home,” said Laura Fitzpatrick, communications coordinator for CRIS-OH.
“The Education, Employment and Empowerment Department at ETSS is so grateful for this partnership and for the support of Alene Candles to provide welcome kits for new Americans who are working hard to increase their English skills and start their careers in the United States,” said Elena Nussbaum, education, employment, and empowerment manager at ETSS.
According to 2021 data , new Americans accounted for nearly 30% of Columbus’ population growth between 2014 and 2019. That same report also showed that immigrants made up more than 10% of the area’s total workforce, contributing significantly to the health of manufacturing jobs in the region.
“At Creating Central Ohio Futures, we strive to give everyone the opportunity to enter the middle class. Tackling this feat truly takes a village, and Alene Candles has been a key member of that village. From providing excellent wages and benefits, to being a steadfast employer partner, to now providing these kits, Alene has truly demonstrated their commitment to the community,” said Bailey Sandin, program manager at CCOHF. “These bags will be used by our cohort participants to offset hygiene costs and make their homes a more welcoming place with a beautifully scented candle.”
Alene Candles Runs for Charity 19 Sep 2023, 6:13 pm
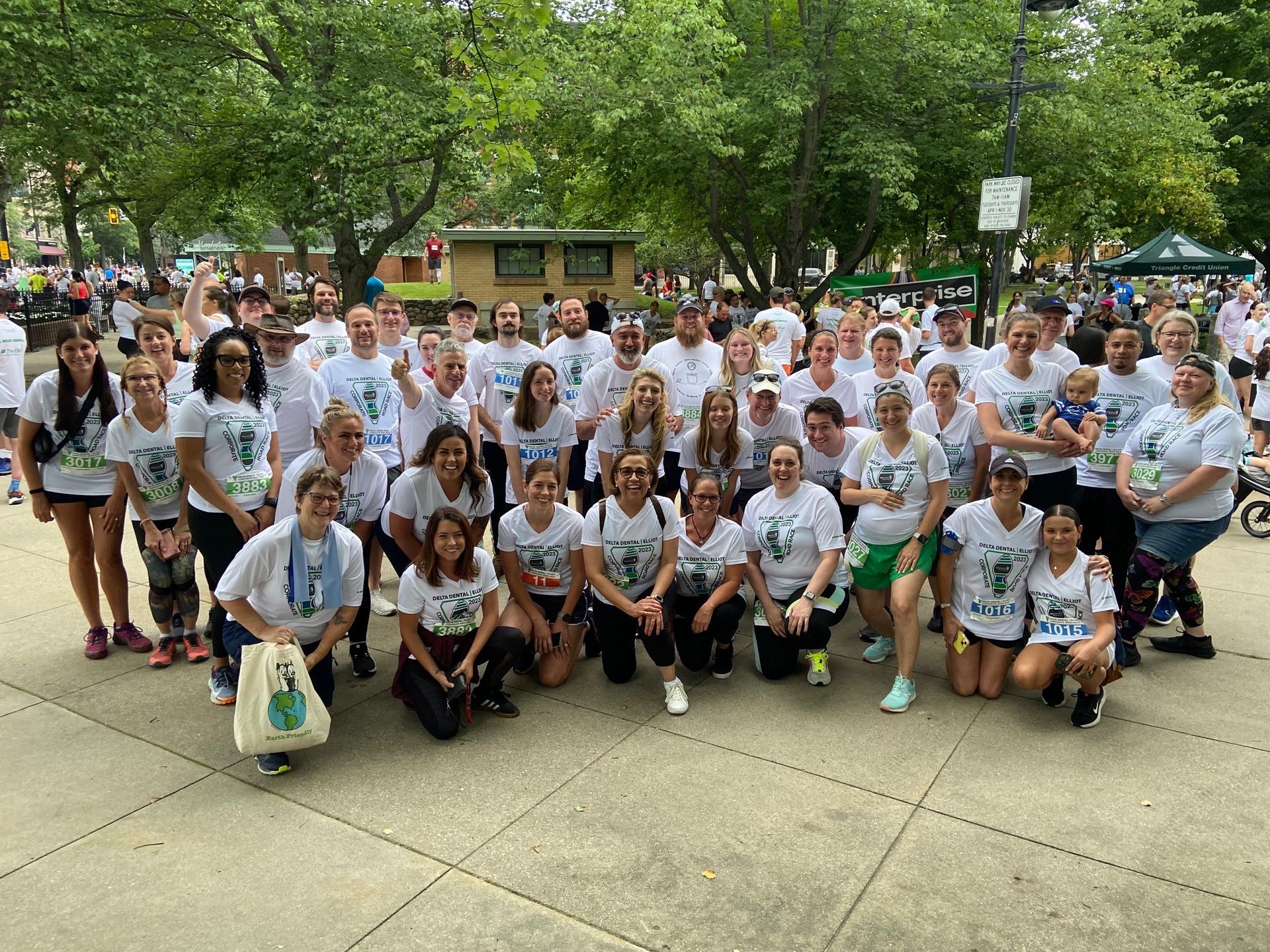
Alene Candles participated in the Delta Dental|Elliot 5K Corporate Road Race on Manchester, NH on Thursday, August 10, 2023. Alene has participated in this race for many years along with other New Hampshire companies. Funds raised from the event benefit the Solinsky Center for Cancer Care at Elliot Hospital including nutrition assistance and programs, rehabilitation therapy, integrative medicine, and support programs for patients as they manage their cancer journey.
Our Alene team ranked #3 in the Top 10 Fundraising Teams! Thank you to everyone who participated in this annual event!
Alene Candles at the 29th Charity Golf Classic 19 Sep 2023, 6:13 pm
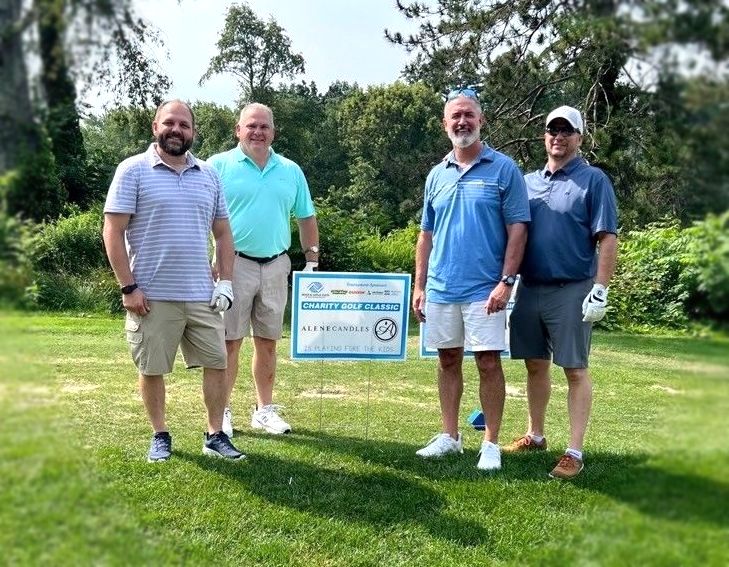
Members of Alene Candles participated in the annual Charity Golf Classic benefiting the Boys and Girls Club of Souhegan Valley on August 10, 2023. The 29th Charity Golf Classic took place at the Amherst Country Club. Alene has participated in this event over the last several years.
Alene Team Members starting on left: Jeremy Putnam, Jim Wood, Brad Colclasure, and Phil Erickson.
For more information on the Boys and Girls Club of Souhegan Valley visit: https://svbgc.org/
Alene Candles Expands Ohio Operations 7 Jul 2022, 5:31 pm
New Hampshire-based company adds manufacturing to existing facility.
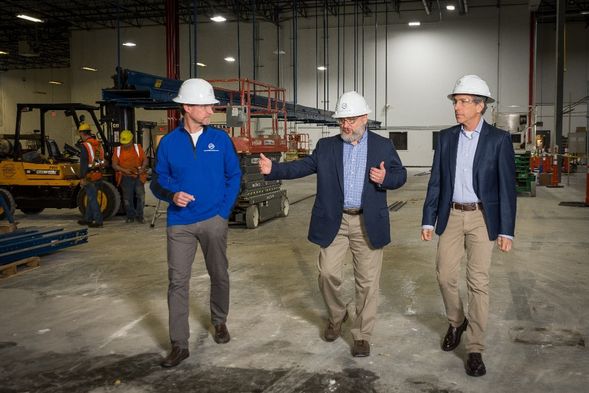
Alene Candles,
a full-service contract and private-label fragrance manufacturer, is expanding its Ohio operations. The company is adding more than 50,000-square-feet to its existing suites, creating a contiguous 230,000+-square-foot manufacturing facility. This will allow Alene Candles to keep pace with demand for its high-quality candles and other high-end custom fragrance products, said the company.
Alene Candles
opened its first New Albany facility in 2012 and expanded operations in October 2020 with the opening of a second manufacturing facility, both located within the New Albany Business Park’s Personal Care and Beauty Innovation Campus. The company is headquartered in Milford, NH. The expansion is expected to be complete later this month.
“Demand for candles rose to unprecedented levels during the pandemic, with individuals spending more time in their homes,” said Rod Harl, president and CEO, Alene Candles. “This expansion is a strategic investment that will allow us to optimize efficiency of our manufacturing processes, while also solidifying our presence in New Albany.”
Alene Candles currently has approximately 700 employees and temporary team members. It said it is currently seeking to hire an additional 100 employees for its peak production season.
Alene Launches Campaign to Support Tornado Victims 13 Dec 2021, 8:45 pm
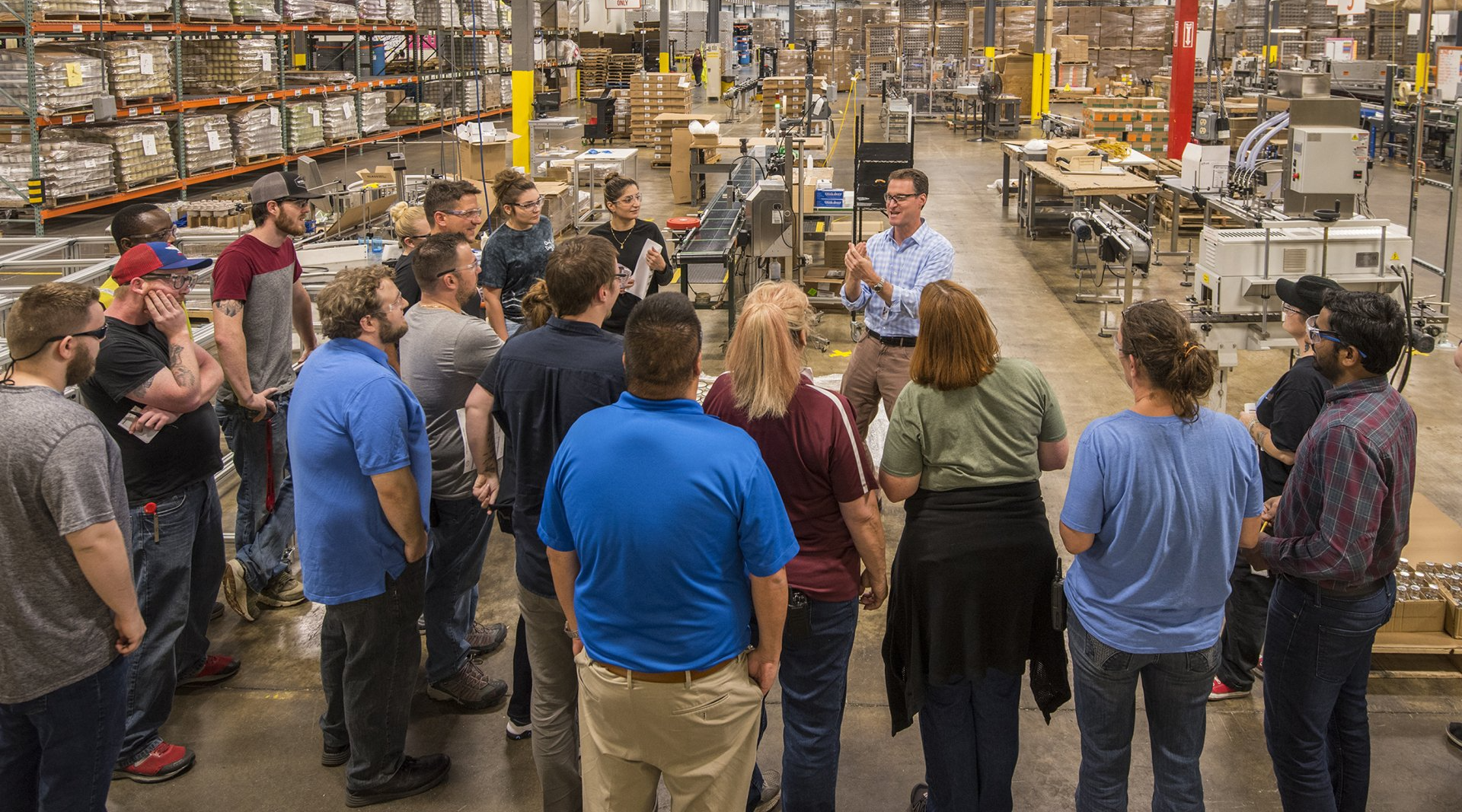
The owners of Alene Candles in Milford have announced a $25,000 donation to support Mayfield Consumer Products (MCP) candle factory employees and their families impacted by Friday’s devastating tornado. In addition to the donations from ownership, the company is matching donations from Alene employees at its Milford, NH and New Albany, Ohio, manufacturing facilities. Alene is also calling on fellow businesses and residents of New Hampshire and Ohio to lend their support to tornado victims.
MCP owners have set up a donation page at www.mcpkentucky.com , where 100% of donations will be given to victim relief. Alene is encouraging employees and the public to make donations and to select the option to “write a note of support” to express that the communities of New Hampshire and Ohio stand with them.
“This is an unspeakable tragedy and we are devastated for the people of Mayfield and our friends at Mayfield Consumer Products,” said Rod Harl, owner, president and CEO of Alene Candles. “The community of candlemakers is a small, tight-knit group. It’s important that our company, employees and community show support for MCP and the town of Mayfield during this difficult time.”
Alene currently has more than 450 full-time employees at its facilities in Milford, New Hampshire, and New Albany, Ohio. This number grows to nearly 1,500 during the holiday season with the addition of seasonal staff.
Mayfield, Kentucky, has a population of 10,000 residents and is roughly the same size as New Albany, Ohio, and slightly smaller than Milford, New Hampshire.
“Despite our geographic differences, there are many similarities between our craft, communities and workers,” said Ted Goldberg, owner and chief business development officer of Alene Candles. “We know our communities of Milford and New Albany will come together to support Mayfield and workers at MCP.”
Congressman Troy Balderson Tours Alene Candles Midwest 14 Oct 2021, 4:52 pm
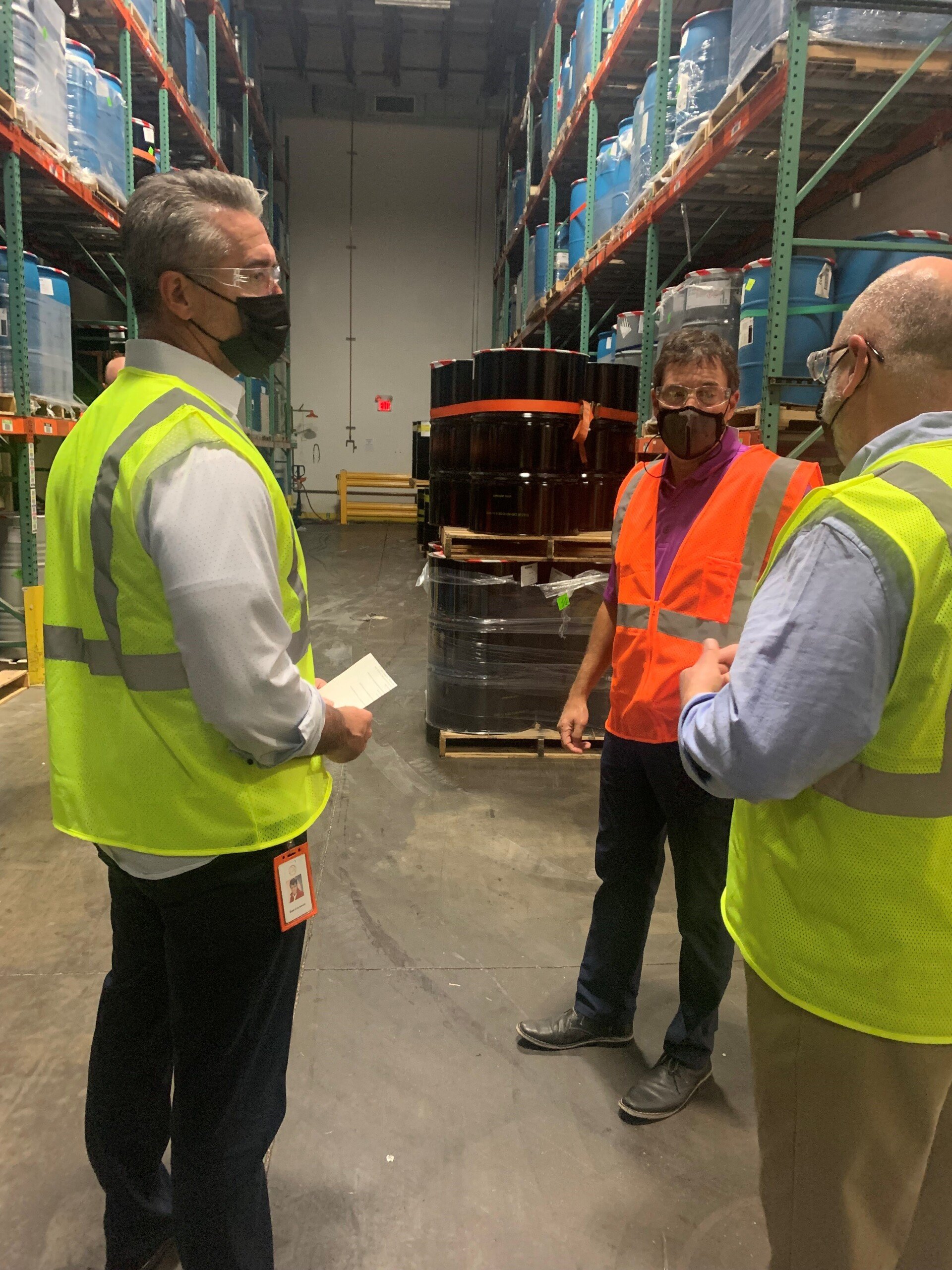
Congressman Troy Balderson (OH-12) toured Alene Candles' manufacturing facility in New Albany, Ohio, to highlight manufacturing month and workforce development in the state.
NH’s Best Companies to Work For Are... 1 Sep 2021, 7:28 pm
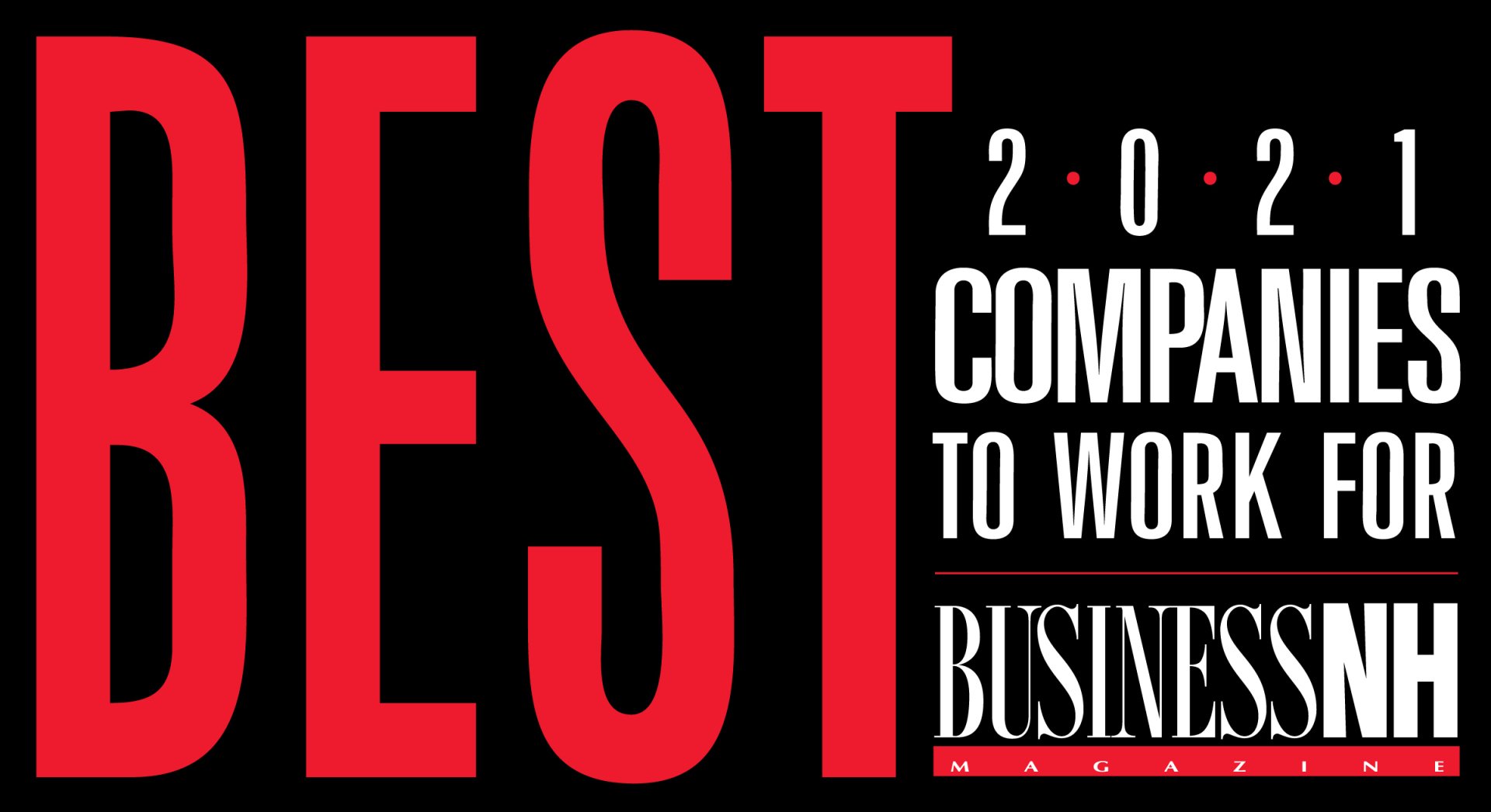
For 24 years, Business NH Magazine has recognized businesses that go out of their way to create engaging workplaces. These are businesses that recognize that a fulfilled employee is more productive. This year’s competition is unique as it also examines how companies adjusted their culture and policies for the pandemic and how they are ensuring that their employee practices are inclusive and equitable for all employees.
The 2021 competition attracted applicants from across the state. Applicants had to have their employees take an engagement survey and they had to complete an extensive employer survey, detailing benefits and workplace practices. Winners were determined from the results of both of those.
Fully, 25 NH companies exceeded the bar of excellence.
The following are the 2021 winning companies:
#1 – Sunrise Labs in Bedford
#2 – Geophysical Survey Systems in Nashua
#3 – Red River in Claremont
#4 – Mascoma Bank in Lebanon
#5 – Lindt & Spr ü ngli USA in Statham
#6 – Novocure in Portsmouth
#7 – Mainstay Technologies in Belmont and Manchester
#8 – Bangor Savings Bank in Portsmouth
#9 – Merchants Fleet in Hooksett
#10 – ITR Economics in Manchester
#11 – CoreMedical Group in Manchester
#12 – The Granite Group in Concord
#13 – CCA Global Partners in Manchester
#14 – Polyonics in Westmoreland
#15 – Bellwether Community Credit Union in Manchester
#16 – Wire Belt Company of America in Londonderry
#17 – Loftware in Portsmouth
#18 – DEW Construction in Keene and Manchester
#19– Boothby Therapy Services in Laconia
#20 – MegaFood in Manchester
#21 – Granite State Credit Union in Manchester
#22 – Sanborn Head & Associates in Concord
#23 – Alene Candles in Milford
#24 – Vapotherm in Exeter
#25 – Cohen Closing & Title in Bedford
To learn about these great companies and the creative ways they attract and retain the best employees possible, their stories are shared in the September issue that is available at www.businessnhmagazine.com/back-issues/september-2021.
Companies that earn a place on the Best Companies to Work For list four out of five years are inducted into the Hall of Fame for two years. Four companies were inducted into the 2021 Hall of Fame: Impax Asset Management in Portsmouth, Klüber Lubrication in Londonderry, Northeast Delta Dental in Concord and Novo Nordisk US Bio Production in Lebanon.
To celebrate the 2021 winners, Business NH Magazine will host the Breakfast with The Best on Sept. 30 at the DoubleTree by Hilton Manchester. (Note this may pivot to a virtual event.) Jermaine Moore, founder of The Mars Hill Group and specialist in diversity, equity and inclusion will give the keynote address, “Helping Your Team Reach New Heights.”
The Breakfast will be held at the DoubleTree by Hilton in downtown Manchester from 8 a.m. to 10 a.m. To register for the event, visit www.businessnhmagazine.com/events/2021-breakfast-with-the-best . (If we have to switch to a virtual event, we will contact people a week before September 30th.
Sponsors of this year’s breakfast are: Best Companies Sponsor: Northeast Delta Dental and Breakfast Sponsor: Merchants Fleet.
For more information on the winners, please contact Editor Matt Mowry at 603-557-9561 or mmowry@BusinessNHmagazine.com. For more information on the event, please call the event manager Kelly Keating Winchester or the events coordinator Vicki Pelczar at 603.626.6354 Extensions 224 and 223 respectively.
Candle company opens second New Hampshire facility 14 Aug 2021, 8:42 pm
This is a subtitle for your new post
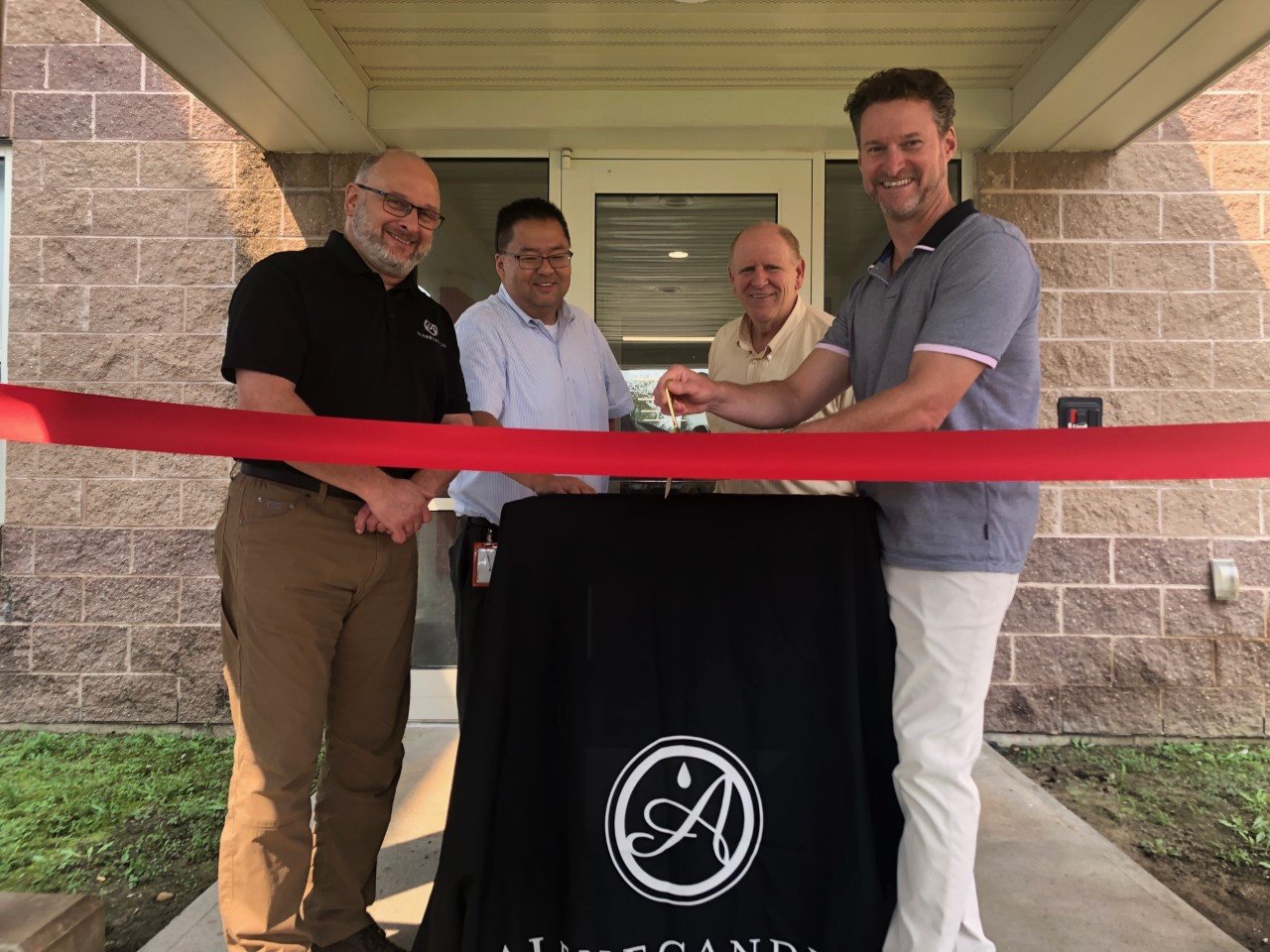
JUST in time for the holiday production rush, Alene Candles of Milford has expanded its operations and opened a new location in Amherst.
“This gives us an opportunity to consolidate closer to home and also support some expansion,” Rod Harl, president and CEO of Alene Candles.
The company worked with a developer from Boston to secure the new facility at 1 Bon Terrain Drive, which provides 200,000 square feet of manufacturing, warehousing and office space for the candle company.
“It has been empty for a few years,” Harl said of the property formerly occupied by the F.W. Webb Company; Alene is occupying about half of the large structure.
Improvements have been underway at the new site since May, and employees began occupying the building earlier this month, according to Harl.
The company’s main campus is still housed in Milford and offers about 170,000 square feet of space among three buildings.
Some of Alene Candle’s off-site storage is now able to be consolidated, and the new space in Amherst provides new capabilities and new opportunities for glass decorating, he said.
The expansion, coupled with the upcoming holiday season, means Alene is seeking additional employees.
“We have hundreds of positions available as we are ramping up for the season,” said Harl, adding dozens of those positions are full-time employment opportunities and not just seasonal posts.
Company-wide, Alene Candles is producing between 500,000 and 1 million candles a day, he said. It has about 350 employees helping to fill production orders.
Alene Candles designs and produces candles for dozens of clients, including well-known retailers such as White Barn and Bath and Body Works, as well as high-end retailers in the New York cosmetics industry. Aside from its headquarters in Milford and its new facility in Amherst, the company also has two sites in Ohio and offices in New York.
Alene Candles was previously named one of New Hampshire’s “Best Companies to Work For” by Business New Hampshire Magazine. It has also been recognized as one of 17 honorees across the country from the TD Bank Thanks You campaign after producing and donating more than 60,000 face shields to more than 200 organizations last summer. Business is robust, despite the pandemic, according to Harl, who said the company’s biggest challenge is filling its workforce.
“We are always looking to hire,” he said.
In addition to Gov. Chris Sununu’s Summer Stipend Program, Alene Candles is offering sign-on bonuses up to $1,200 for some critical, permanent positions, according to a release.
Sununu announced his summer stipend initiative in May, which was created to coincide with the state’s decision to end federal pandemic unemployment benefits.
New Hampshire company offers incentives to employees to increase vaccination rate 12 Aug 2021, 8:37 pm
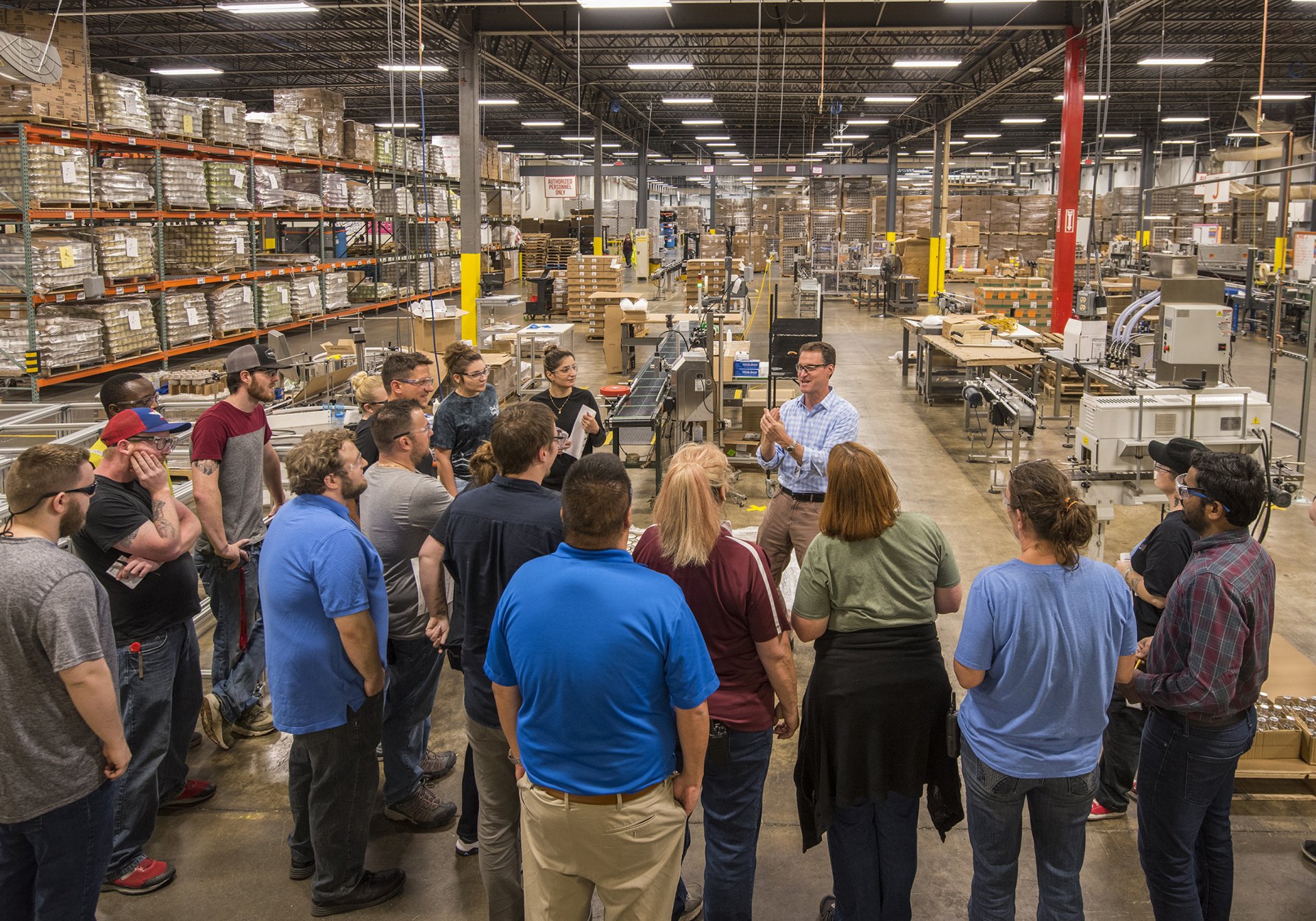
MILFORD, N.H. — A New Hampshire company has increased incentives in hopes of increasing the vaccination rate among its employees. The CEO told News 9 he has upped the ante as the delta variant spreads.
Based out of Milford, Alene Candles pivoted production in the early parts of the pandemic to create face shields. The company kept hundreds of people employed between New Hampshire and Ohio.
“Since vaccines have been available we really mounted an education campaign to enable all our employees to have the information they need to get comfortable in pursuing a vaccine,” CEO Rod Harl said.
Crafting an easily digestible vaccine message is a delicate act. To encourage employees to get a shot, Alene has offered paid time off for vaccine appointments, gift cards for proof of vaccination and set up on-site vaccine clinics.
The company also hosted a roundtable discussion with a doctor from Dartmouth-Hitchcock Medical Center who fielded questions in multiple languages.
“They may be collecting rumors or hearsay from other folks. So, bringing in a medical professional that can speak to people in their own language and can answer questions of all types and not pass any judgment. That’s a resource I was thrilled to provide,” Harl said.
Despite their efforts, he said they have experienced community spread at the Ohio facility, nothing significant has happened in the Granite State.
“At the end of the day, there are companies who took risks with their employees and made some decisions that we chose not to make in the interest of our partners and business really,” Harl said.
At the New Hampshire facility, social distancing has been maintained and masking has been optional, but Alene believes that could change if the delta variant runs rampant in the state.
Governor Sununu Visits Alene Candles as They Seek to Hire 250+ Workers 11 Jun 2021, 6:02 pm
Nation’s leading contract candle manufacturer set to hire 250+ seasonal and full-time employees amid labor shortage and heading into its summer busy season.
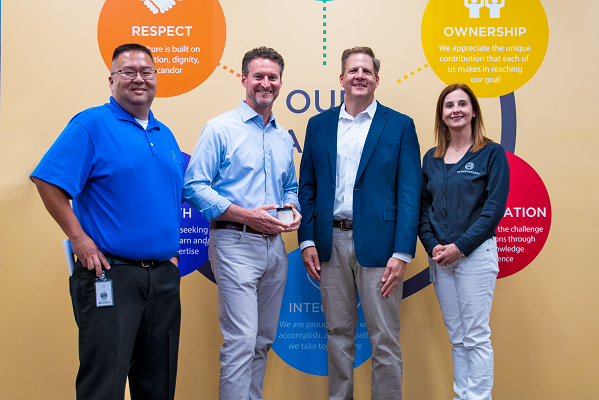
Governor Christopher T. Sununu toured Alene Candles on Friday, June 11, to address workforce challenges in the manufacturing industry and spoke with the company’s CEO, Rod Harl, about efforts to support workforce recruitment in New Hampshire.
Alene Candles is one of the nation’s largest contract candle manufacturers and is currently facing a labor shortage as production ramps up in the summer, in preparation for the holiday season.
Alene Candles is actively looking to fill open positions, with 57 full time and 200 seasonal positions currently open in New Hampshire alone, and more than 500 openings between their New Hampshire and Ohio facilities.
Governor Sununu also spoke about his recently announced Summer Stipend Program – Return to Work Bonus as a replacement for the unemployment benefit. Alene Candles is offering additional bonuses of up to $1,200 to new employees.
Alene Candles seeks to hire 400, offers $1,200 signing bonus, three-day work week 20 May 2021, 5:20 pm
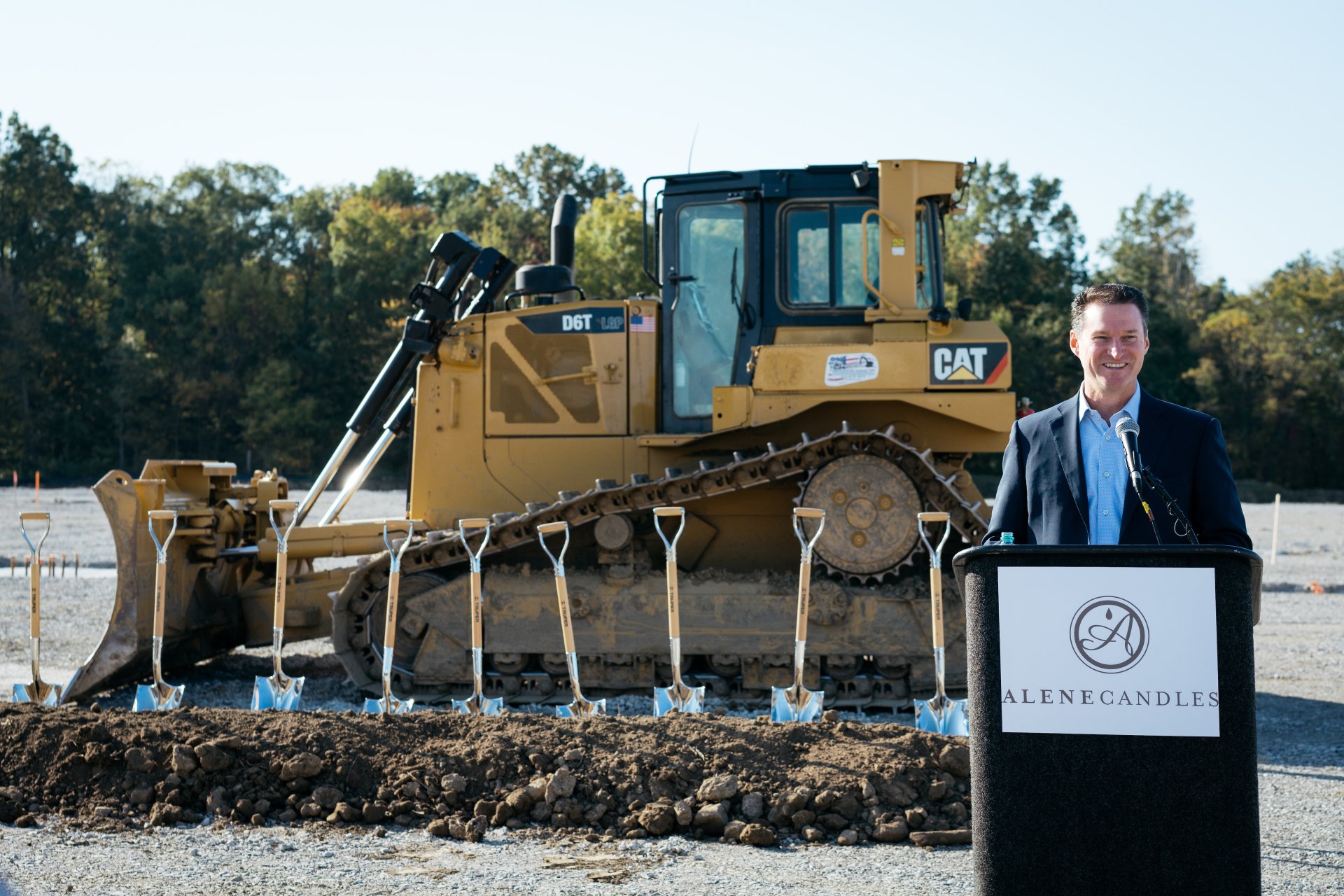
NEW ALBANY -- Alene Candles, like many companies, is so desperate for employees at its New Albany facility, it not only offers new hires a job, but also a $1,200 signing bonus and four days off a week.
The New Hampshire-based company, which opened its Licking County facility in 2012 and expanded in 2019, announced in April it seeks to hire 400 for its operation in the New Albany Personal Care and Beauty Campus, including 300 candlemakers for seasonal work and 100 full-time, year-round positions.
Rod Harl, company president and CEO, said Tuesday there are still 80 open skilled positions and almost 200 factory positions available. The sign-on bonuses are for certain positions and a restructured shift schedule allows employees to work a three-day, 36-hour week with a minimum hourly rate of $14.50.
The company, one of the nation’s leading contract and private-label candle manufacturers, will increase starting salaries and hourly pay for all employees so everyone earns the equivalent of the 40-hour week previously worked while still enjoying four-day weekends. It has 200 full-time employees and 600 total.
"We need people now," Harl said. "We need people not just to sign on, but stay with us. We’d like to hire people, even temporary, looking for a full-time job. We’re adding people every week, but it’s a challenge.”
Ohio Means Jobs/Licking County workforce development administrator Angela Carnahan said many employers are using incentives such as signing bonuses, retention bonuses, referral incentives for current employees and wages increases.
A $300 weekly supplement to unemployment benefits will end in late June. Last year, unemployed received a $600 weekly supplement ending in late July/early August.
Harl said he believes the supplements to unemployment have delayed some people from returning to work, but Licking County's March unemployment was 3.8%, down from 4.7% in March 2020. Two years ago, the county's unemployment was 3.6%.
"Last year, we offered $600 bonus to come in early," Harl said. "We saw a change in applications. We’re seeing a similar phenomenon this year. It’s bringing people in, but we still are struggling.”
Alene Candles' productivity in 2020 eclipsed its 2019 numbers, despite closing its factory for several months to produce face shields for medical personnel and first responders. The company paid all of its 200 New Albany employees during the shutdown, but 20 to 25 employees volunteered to come in to make the face shields.
Two-thirds of its candles sold are in the second half of the year, and 40 percent in the fourth quarter. The company's growth is expected to continue into 2022.
“We’re finding our customers are asking us for as much product as we can turn out, even though it’s not typical holiday season," Harl said. "It’s the highest demand, at this time of year, we’ve ever seen.”
Alene Candles began manufacturing in a 100,000-square foot space in a multi-tenant building at the New Albany campus in 2012. Then, in October 2019, it broke ground on a $30 million, 280,000-square foot warehouse a mile from its manufacturing facility.
Harl said he's not sure if fear of COVID has kept job seekers away, but said the company has a good safety record.
“It’s tough to tell," Harl said. "We’ve had good success internally. There's no evidence of community transmission on site. We’ve let people go because they're not following safety protocols. Those following the rules have not gotten sick.
“I’d probably say child care, that may be a bigger impediment than fear (of COVID) at this point. We’re also looking at transportation, a bus service to serve people living some distance away, at a reduced or low cost."
He said the Newark-Granville market is important to the company, which also depends on immigrant workers, enjoying a good relationship with the Somalia community. Still, finding workers is a problem not likely going away, he said.
The county's workforce of 91,300 and employment of 87,900 is more than March of 2020 or March of 2019. There were 3,400 unemployed in Licking County in March, down from 4,300 the previous year.
“We knew the location of New Albany would, in time, be challenging for attracting workers, but it’s terrific from a supply chain and integration with other suppliers," Harl said.
“The central Ohio focus has been on attracting companies that create jobs, and that’s terrific for our economic development. But, it's time to get people to move (here). We’d love to help attract people to central Ohio.”
New Albany candle facility looking to fill 400 positions as peak production season nears 12 May 2021, 5:39 pm
Peak production season for Alene Candles takes place each summer, as the company braces for a high volume of orders ahead of the holidays.
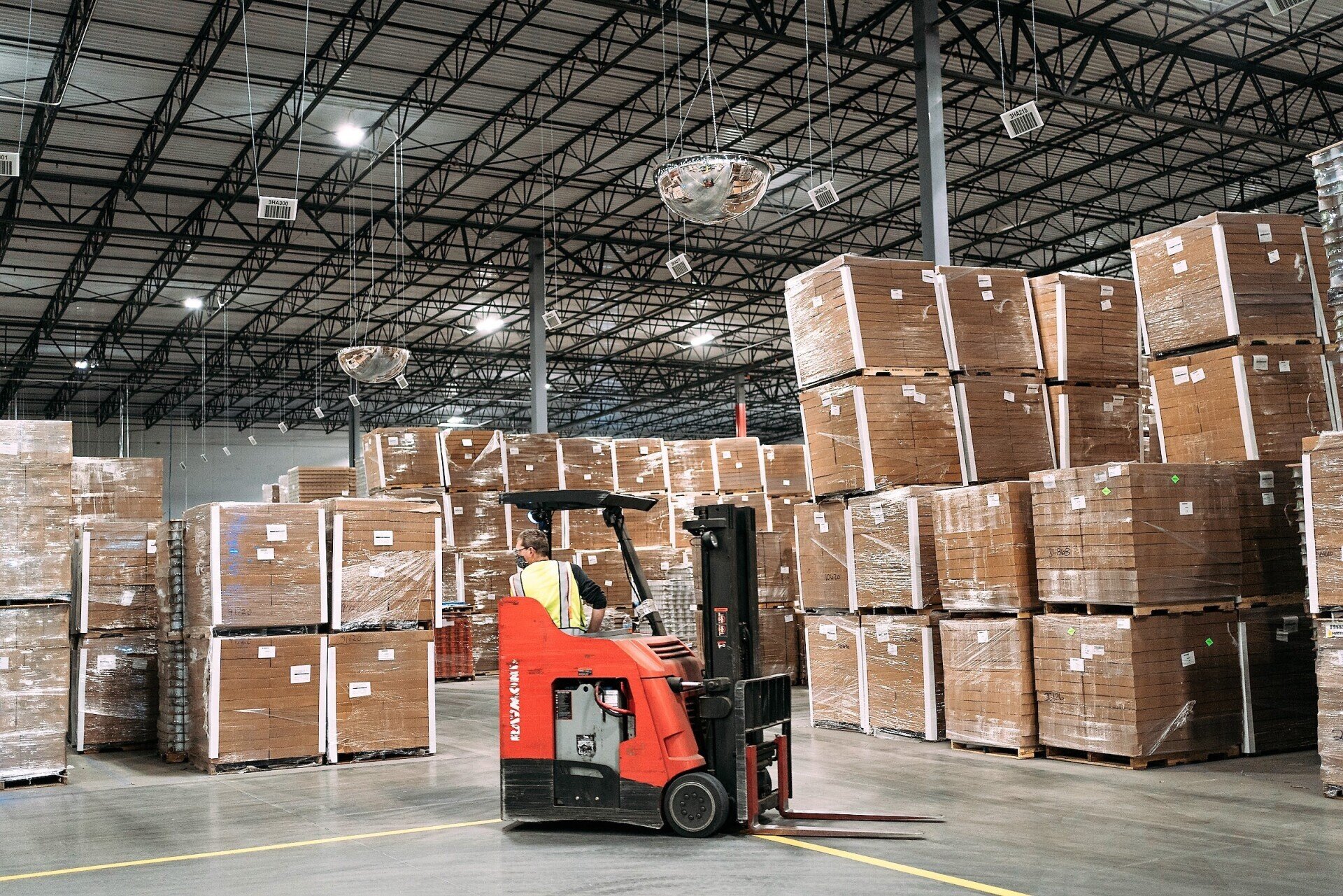
NEW ALBANY, Ohio — A nationally known candle company is ramping up for this summer’s peak production season, and is looking to fill over 400 positions at its New Albany facility.
While many businesses took a hit during the pandemic, Alene Candles saw an increase in demand with stay-at-home orders in effect.
“With more people working from home, we produced more candles over the course of last year than we did in all of 2019,” said Rodney Harl, the manufacturer’s president and CEO. “We are projected to carry this momentum through the summer and upcoming holiday season, requiring significant growth for our team.”
The company is looking to fill 300 seasonal positions over the course of the next two months, and an additional 100 full-time positions year round, according to a release.
Shifts will consist of three, 12-hour work days a week, followed by four consecutive days off. Additionally, Alene Candles says it has increased wages for employees who were previously working 40 hours a week to make up for lost hours.
Peak production season for Alene Candles takes place each summer, as the company braces for a high volume of orders ahead of the holidays.
The company briefly shut its facility down in 2020 to aid with PPE production. Despite this, Alene Candles still saw an increase in production in comparison to the previous year, according to the release.
“We have always been committed to supporting our team members and have incorporated additional workplace enhancements and benefits to enable us to produce best-in-class candles for our retailers nationwide,” said Harl.
Those looking to apply must have a high school diploma or general education degree, it reads in the release. You can apply here.
Alene Candles honors local leaders as ‘Milford Luminaries’ 26 Sep 2020, 3:18 pm
Alene Candles, for the second year in a row, is praising those in the community who have given back helping families, friends and neighbors.
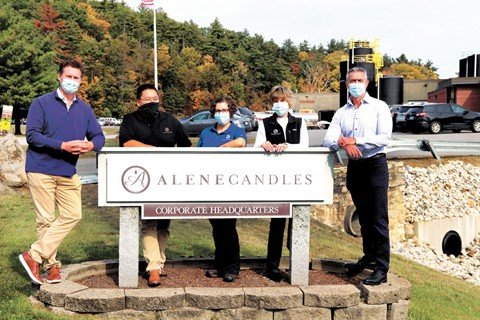
Pivoting to Making Masks 9 Jul 2020, 6:43 pm
Alene Candles in Milford and Peak Achievement Athletics in Exeter turned from producing candles and athletic equipment respectively to crafting face shields.
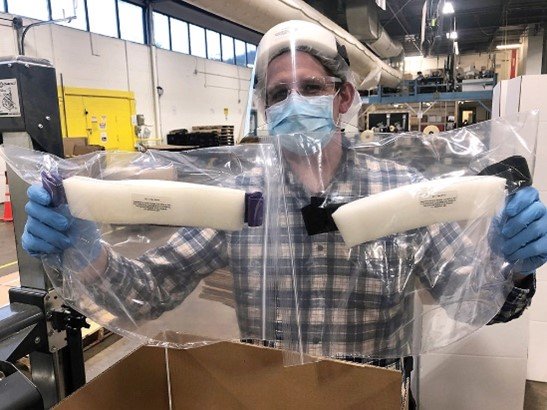
MILFORD, NH - With medical personnel and first responders in desperate need of personal protective equipment, Alene Candles in Milford and Peak Achievement Athletics in Exeter turned from producing candles and athletic equipment respectively to crafting face shields.
To date, Alene has made 30,000 face shields in NH and 30,000 in its Ohio facility. “I’m so incredibly proud of our team for banding together to give back to those in the community who are working on the front line to battle the coronavirus pandemic,” says Rod Harl, president and CEO of Alene. “In just seven days, we went from an idea about how we can harness our resources to positively impact the greater good to producing face shields and delivering them to hundreds of community organizations. We are thankful that we can play a role in fighting this pandemic, no matter how small.”
Company leaders brainstormed ways to put manufacturing resources to use during the pandemic. After having discussions with several industry peers, Alene located a face shield design from John Hopkins University and then got to work identifying suppliers, eventually partnering with Thermoformed Plastics of New England in Biddeford, Maine.
Early in the pandemic, Peak Achievement Athletics, the parent company of Bauer Hockey, Easton Baseball/Softball, Cascade Lacrosse and Maverik Lacrosse, was able to shift production to medical-grade masks at the Cascade and Bauer manufacturing center in Liverpool, NY as well as at the Bauer Innovation Center in Blainville, Quebec.
“Our team is built around an athlete’s mentality and the ways we can enhance performance and protection. We viewed the virus as the competition. When this pandemic hit, it was a natural shift to figure out how we can fight back and help the larger cause,” says Ed Kinnaly, CEO of Peak Achievement Athletics.
When orders topped one million, the company shared the manufacturing instructions online making it possible for other firms to join the effort.
“I’m so proud of the way our team responded. We pivoted almost instantaneously to manufacture medical shields. It didn’t take long for orders to exceed capacity, so we made our designs and supplier info public,” says Kinnaly. “Through the media, we urged other manufacturers to step up and help us protect the medical community on the front lines helping others despite not having proper equipment. In the end, we viewed it as a part of our ‘One Team’ mission.”
For more information, visit alene.com and bauer.com
https://www.businessnhmagazine.com/article/pivoting-to-making-masks
New Albany business park manufacturers switch gears during pandemic 27 Apr 2020, 2:45 pm
For a little while at least, a candle-manufacturing company in New Albany is trying something new.
NEW ALBANY - Alene Candles, 8860 Smith’s Mill Road in the New Albany International Business Park, suspended its candle-manufacturing operations in mid-March because of the COVID-19 coronavirus pandemic, said plant manager Darrell Finck.
But manufacturing at the facility has been going strong once again, as staff members work hard to produce plastic face shields instead of candles.
Finck said the company plans to make 40,000 face shields for health-care workers to use with masks they wear. He said he is proud of employees, who are voluntarily stepping up.
“It’s definitely inspiring,” he said.
Alene Candles has not been alone in its efforts.
Other companies in the New Albany International Business Park have been stepping up to provide supplies for those on the front lines of the pandemic. They include Bocchi Laboratories’ pivot to manufacturing hand sanitizer and Exhibitpro’s collaboration with a Phoenix, Arizona, engineering firm to produce face shields.
Alene’s production of face shields began April 9, Finck said.
After the company stopped its candle production, leaders soon began discussing how the company could help during the pandemic, he said. They settled on the design and manufacturing of face shields.
Using a design from Johns Hopkins University, engineering teams worked on a way for the facility to produce them, Finck said.
The plastic shield extends from the forehead to below the chin, and a strip of material provides padding for the wearer’s forehead, he said. The shield is secured with an elastic band around the head and is designed to fit over a mask.
The company’s 250 employees still are on payroll, Finck said, and nearly 20 employees are voluntarily working to produce the shields.
As of April 16, Alene had produced 10,000 shields, Finck said. A variety of organizations and businesses are using them, including local fire departments, ambulance services, dental and surgical practices and first responders, he said.
Exhibitpro at 8900 Smith’s Mill Road N. also has been making face shields.
The company is an experiential marketing firm that specializes in designing and fabricating trade-show exhibits, events and branded environments, said Blake Miller, director of sales.
But the firm went in another direction to provide 200 face shields for the Mayo Clinic in Phoenix.
The initiative originated from conversations CEO Lori Miller had with her daughter, Shae Saint-Amor, a Mayo Clinic employee, about the lack of personal-protective equipment for staff members, Miller said.
Exhibitpro was able to partner with Phoenix engineering firm Augspurger Komm Engineering, where Shae Saint-Amor’s husband, Justin Saint-Amor, works, Miller said.
Exhibitpro was able to cut plastic the business already had into the shape of shields, and the engineering firm 3D printed a band that connects the shield to the wearer’s head, Miller said.
The first shipment of face shields to the Mayo Clinic was April 15, and the second was April 24, Miller said.
Less than a half mile down the road from Exhibitpro, Bocchi Laboratories, at 9200 Smith’s Mill Road, has been making hand sanitizer.
Under normal circumstances, Bocchi is a contract manufacturer that makes many products for customers, said Elena Olivieri, vice president and general manager.
Some of the cosmetic products were alcohol-based, and Bocchi was able to begin producing hand sanitizer, she said.
Bocchi is manufacturing little to no other products, Olivieri said.
“We’re having to react to the supply chain,” she said.
About 70 people across multiple shifts are producing the sanitizer, and they are working voluntarily, Olivieri said. Other workers are at home, but all staff members still are on the payroll, she said.
Bocchi is producing 2-ounce bottles of sanitizer, as well as gallon containers for industrial use, Olivieri said. Customers provide the bottles, she said.
“We’re trying to hit all the markets as best we can,” she said.
Both new and old customers, from Ohio and beyond, have been reaching out for sanitizer, Olivieri said.
The company also is making 5,000 bottles of sanitizer to donate to central Ohio organizations, she said.
Olivieri said Bocchi wants to produce sanitizer for as long as possible. At some point, stores will reopen, and then the company will have to help the retail industry get back on its feet, she said.
https://www.thisweeknews.com/news/20200427/new-albany-business-park-manufacturers-switch-gears-during-pandemic
Coronavirus: Alene Candles shifts to production of face shields at Licking County facility 21 Apr 2020, 2:13 pm
Alene Candles suspended its candle-making operation at the New Albany Personal Care and Beauty Campus, but still manages to brighten up the day for those receiving its latest product.
NEW ALBANY - The New Hampshire-based company, which opened its LickingCounty facility in 2012, started making face shields for medical personnel andfirst responders after the temporary shutdown of the non-essential businessduring the coronavirus pandemic.
The company continues to pay all of its 200 New Albanyemployees during the pandemic, but 20 to 25 employees volunteered to come towork to make the face shields.
“Our team could not sit by while doctors, nurses and firstresponders do everything they can to combat the coronavirus pandemic, allwithout enough personal protective equipment to keep them safe,” said Rod Harl,President and CEO of Alene Candles.
Company leaders searched for ways to put its manufacturingresources to use during the pandemic. They saw the need of health careproviders, located a face shield design from Johns Hopkins University andtransformed its production facility for the new purpose.
Darrell Finck, the New Albany plant manager, said, "Wethought about how we comply with social distancing in the future and once wefelt comfortable doing that, we brought people in and made this process work.
"Our supply chain team really went out after findingour material. We shifted some of our work stations around in the plant.Everybody here is doing this because they want to do more."
The company set a goal to manufacture 40,000 face shields,and made 15,000 in one week of production.
Alene Candles donated face shields to Consumer SupportServices, Licking County Board of Developmental Disabilities, Newark ResidentHomes and Center for Dental Health, all in Licking County, as well as theFranklin County Sheriff's Department, among about 30 others.
Finck said the work has been very gratifying.
"They're coming to our facility and picking themup," Finck said. "It's been great, everybody coming in very upbeat,very positive. Extremely rewarding."
The company may bring more employees back if it continues toramp up face shield production. Its Milford, New Hampshire facility will alsomake 40,000 shields.
“We have highly technical manufacturing capabilities and atalented team that’s ready to help however we can,” Harl said. “I am incrediblyproud of our team for jumping to action; we are thankful that we can play arole in fighting this pandemic, no matter how small.”
To request face shields produced by Alene Candles , contactfaceshields@alene.com. For more information about Alene Candles, visit www.alene.com .
Milford candle company switches production to face shields for medical workers 1 Apr 2020, 2:54 pm
Thousands of critically needed face shields are being made at a candle company in Milford after the company was able to switch its production in seven days.
Candle company now working to produce 10,000 face shields 31 Mar 2020, 3:02 pm
Alene Candles has temporarily halted its candle-making and is now in the process of manufacturing thousands of face shields for medical professionals in New Hampshire and Maine.
MILFORD - “I don’t know that any of us imagined acircumstance like we are in now,” said Rod Harl, president and CEO of AleneCandles in Milford.
As first responders and health care facilitiesthroughout the nation continue seeking personal protective equipment in lightof the COVID-19 pandemic, Harl said his company could not sit by quietly. AleneCandles explored different ways to assist, and ultimately determined that itcould produce plastic face shields to protect doctors, nurses and other healthcare providers.
“Our engineers worked on procedures on how todo the assembly, so everyone had clear work instructions. It did take a littlebit of hands-on training for our supervisors, but once we had it going theywere able to engage in the manufacturing process,” Harl said on Tuesday.
The Milford facility is utilizing a faceshield design from Johns Hopkins University, and has secured raw materials fromThermoformed Plastics of New England in Biddeford, Maine, which has donated thesupplies. Production began Monday at Alene Candles.
However, the company ran out of some necessarysupplies and was forced to wait until Tuesday afternoon to resume its assemblyline once additional supplies arrived. It expects to donate 10,000 face shieldsnext week to emergency workers and health professionals in New Hampshire andMaine.
As Alene Candles continues to pay itsemployees even though production of candles has stopped, Harl said about 20workers arrived on Monday to volunteer their services to make the face shields.Knowing there is a critical shortage of personal protective equipment, severalemployees want to help out and do something for the greater good of thecommunity, he said.
Joshua Rowsey, a process technician at AleneCandles, said his fiancé currently works as a health unit coordinator in theemergency room at Southern New Hampshire Medical Center in Nashua; both of herparents, who are retired from the medical field, are now back at work.
“This face shield project allows me to giveback as well,” said Rowsey, adding he was ready to get out of the house.
“I've been home from work for a week and I wasgetting bored,” he said. “I’ve finished the projects I had to complete at home.This was a good opportunity to get back to work.”
Candle company to build warehouse near its New Albany factory 15 Oct 2019, 7:27 pm
Alene Candles broke ground Tuesday on a $30 million warehouse in New Albany that will complement its nearby factory.
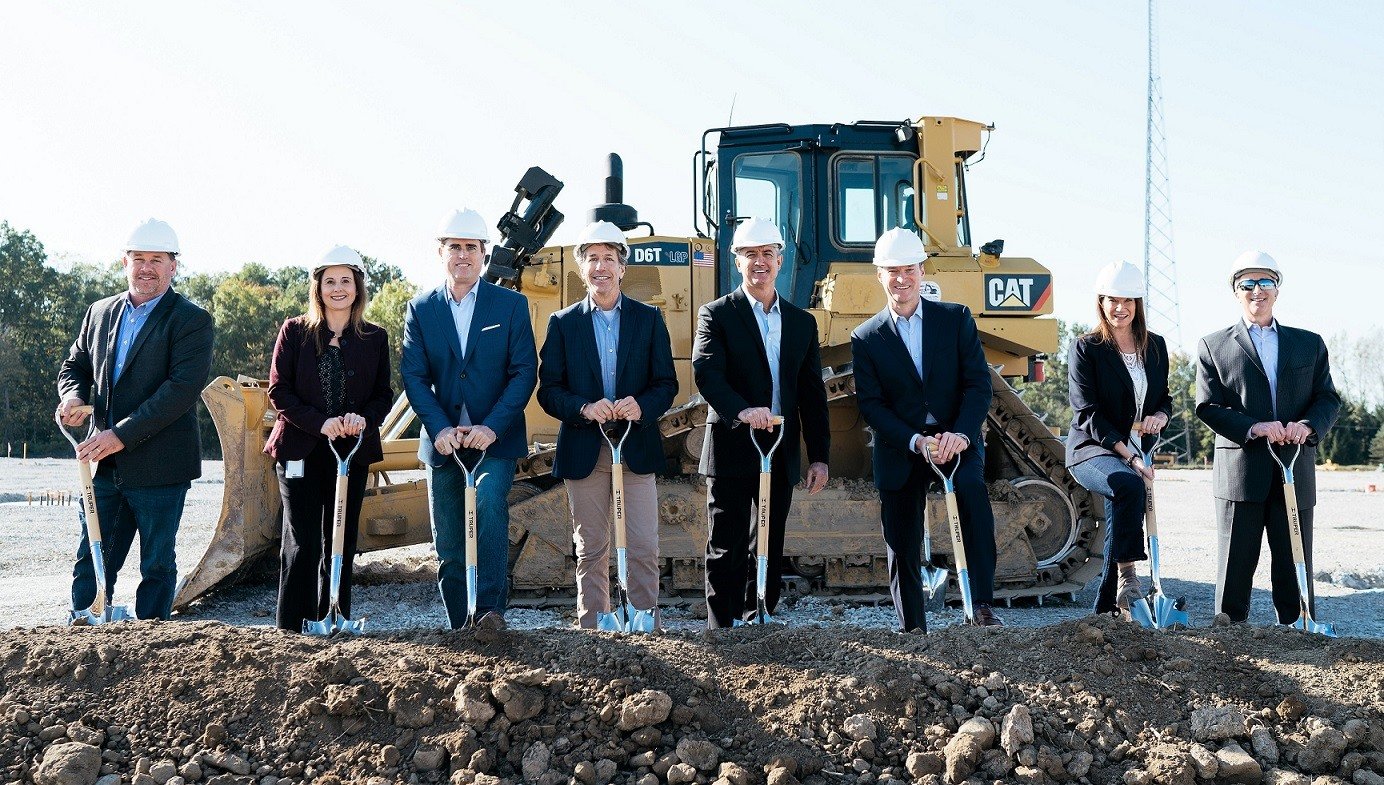
Getting Ready For The Holidays 23 Sep 2019, 1:38 pm
Alene Candles makes call for help
September 23, 2019 - UNION LEADER
MILFORD — As summer comes to a close, Alene Candles is ramping up its production in preparation for the holiday season.
Hundreds of extra workers have been hired to help with the influx of orders, and the company is eager to make the most of the 93 days remaining until Christmas.
“This week we have up to 11 production lines running and about 425 employees helping out,” said Evan Fish, plant manager at Alene Candles, 51 Scarborough Lane.
Alene Candles typically employs 200 workers year-round, but takes on additional hires during the fourth quarter of the year.
“We have grown a lot. We make seven times more candles now than when we bought the business in 2008,” said Rod Harl, president of Alene Candles. “We have reinvented the company considerably.”
Alene Candles designs and produces candles for dozens of clients, including well-known retailers such as White Barn and Bath and Body Works, as well as high-end retailers in the New York cosmetics industry. Its headquarters includes a 180,000-square-feet facility in Milford, but the company also has a factory in Ohio and offices in New York.
Last week, thousands of candles were poured, perfected, packed and shipped from the Milford site.
“We have some customers with a very rapid supply chain. We can get their orders and have them in the stores three weeks later,” Harl said.
Large silos are stationed outside of the Milford plant, which hold massive amounts of molten wax. The wax is combined with fragrances and color additives in the mezzanine level of the facility, which is mixed inside of 30 dairy tanks before traveling to the lower level production floor.
Once on the main level, machines place the wicks into vessels where they are secured in typical glass candle containers. The wax is then poured into the containers before the product solidifies and travels down the manufacturing line where workers align the tips of the wicks, clean the outside of the containers and package the candles into boxes.
They are then placed onto pallets and ready for shipment, according to Harl.
Vanilla, pumpkin, spice and pine-based fragrances are popular during this time of year, according to workers.
“We are doing such high volume right now,” Harl said. “We have this systemized to a science.”
With the unemployment rate so low in New Hampshire, Harl acknowledges that it can sometimes be difficult to find extra seasonal work. However, he says several of his workers have been with the company longer than him. Most employees reside in southern New Hampshire or northern Massachusetts.
Aside from the manufacturing line, Alene Candles also has a research and development lab, analytical lab and burn lab where experiments are conducted on different scents, materials are tested and workers ensure that the custom products are burning reliably, safely and consistently, Harl said.
Alene Candles was founded in 1995, and up to 1 billion candles have been distributed since its inception.
“We make good quality products that sell well, and we are always looking for new and interesting ideas,” he said.
About two-thirds of the company’s sales will be completed during the second half of this year, with about 40 percent of its overall production taking place in the fourth quarter, according to Harl. By February, the company will be back to its typical 200-person workforce.
Alene Candles is also working to expand its community involvement. It recently launched a new program to honor Milford community leaders and provide additional resources to area nonprofits. Alene’s Milford Luminaries program will recognize four outstanding individuals for their contributions to the Milford community through their jobs or volunteer work. As part of the program, the company will contribute $4,000 to local nonprofits.
Alene Candles awards annual $500 scholarship 20 Jun 2019, 12:00 am
June 20, 2019 – NASHUA TELEGRAPH
MILFORD – In an effort to promote the next generation of scientists and engineers, Alene Candles, a company with operations in Milford, recently awarded Milford High School graduating senior Keon Jackson a $500 scholarship.
This scholarship will help Jackson as he heads to Nashua Community College in the fall to begin his pursuit of a bachelor’s degree in network engineering.
Jackson received the award during a presentation at his school earlier this month. Jackson is the son of Saicha Pacheco, a production lead at Alene Candles. Pacheco has served in this position for five years. She expressed gratitude for Jackson’s scholarship.
“The scholarship will help because it helps financially,” Pacheco said. “He is planning on getting a bachelor’s degree. Any bit of help is awesome.”
She added, “I’m very, very thankful that they’re willing to help me out like that. I think it’s great. It’s a very sweet and thoughtful thing that out of all the applicants, they chose (Keon).”
Company President Rod Harl stated, “This year, we’re pleased to award Keon Jackson with a scholarship.
His mother has made countless contributions to the organization. We know that Keon will do the same in the future, wherever his path may lead.”
According to Alene officials, Jackson’s application immediately stood out, as he wrote about his desire to work hard, and to make his mother proud by graduating from college.
He also stood out with his teamwork and goal-setting mentality and his volunteer work within his community.
This is the eighth year the company awarded a Milford graduating senior with a scholarship. Alene Candles Director of Human Resources Heidi Ebol said every year, the pool of applicants has gotten larger and larger.
Ebol said officials look at several areas when selecting a student for a scholarship.
She said they prefer to support students who are interested in pursuing science, technology, engineering, art and math (STEAM).
They also take into account grades and who may get other scholarships.
There’s also an essay, she said, which they weigh heavily. Ebol said it great to support both Jackson and Pacheco.
Igniting interest 1 Jun 2019, 12:00 am
Students tour candle factory
June 1, 2019 NASHUA TELEGRAPH
MILFORD – Boys & Girls Club of Souhegan Valley science, technology, engineering, art and math (STEAM) students saw where their passions could take them, Friday, by touring Alene Candles in Milford.
Each year, the company produces millions of candles for popular retail brands. This was the second time this week that students from the Souhegan Valley club visited.
The club offers a number of different STEAM-related areas for students to experience, including:
• Design and Engineering, during which students design and build towers, bridges and other models;
• Experimentation and Demonstration, through which students build experiments such as bottle rockets and electromagnets;
• Theater Stagecraft, wherein students can help design and build theatrical sets; and
• Stop Motion Animation, which allows students to develop an idea, create a storyboard and then a film.
In addition, students can also access the club’s Lego corner, makerspace “Creation Station,” and Chromebooks and tablets.
“Our goal is to provide a welcoming environment for kids to get involved in hands-on, experience-based learning and fun. It’s a place where ideas can be conjured up and put into action. Ingenuity and activity are highly encouraged,” it notes on the club’s website.
Friday, students toured the Alene Candles facility and got to walk through the company’s various labs. During the tour, the students filled candle jars with wax, practiced thermal readings and learned the chemistry behind the wax.
Once students were done with their tour, they were able to reflect with Alene Candle workers on what they had learned.
Alene Candles Lab Manager Peggy LaFrance, who has worked for the company for 17 years, said she never thought growing up that she would end up working with candles. She never had the opportunity to visit a candle factory and see what happens behind the scenes, as the club members did Friday.
“Now you’ve had the opportunity to see what happens at candle factories. You might work here,” LaFrance said, adding that there were all kinds of different jobs within their company.
“Sometimes, you have to think outside of the box of what you want to do,” LaFrance told the students. “It’s a choice. You’re young; you’re in the STEAM program; you’re learning things. Keep your mind open.”
Jackson G. a fifth-grade student, exclaimed, “Forget about working at the zoo. I’m going to work for candles.”
Mike McKnight, the students’ teacher, said at the Boys & Girls Club of Souhegan Valley, they focus on providing opportunities for the kids and giving them exposure.
“They get a lot more hands-on opportunities, if they want it, as they get older,” he added.
Regarding the tours, McKnight said, “This is good because we get to see real-life science in action, rather than somebody talking about it. You get to see it happening.”
Alene Candles donates $10K 11 Apr 2019, 12:00 am
April 11, 2019 – MILFORD CABINET
MILFORD – Building on its longstanding commitment to local community organizations, Alene Candles recently donated $10,000 to the Boys & GirlsClub of Souhegan Valley. These funds will be used to bolster the organization’s well-regarded Science, Technology, Engineering, Arts and Mathematics (STEAM)program, including purchasing new equipment and providing unique, hands-on experiences for program participants.
“As a fellow member of the Milford area community, we thought it was extremely important to help members of the Boys & Girls Club develop a love for math and science,” said Rod Harl, president of Alene Candles. “Many of our scientists and engineers were introduced to their fields early on, following their passions to pursue higher education and secure meaningful work. This donation will allow countless Boys & Girls Club participants todo the same.”
The BGCSV primarily services communities in the Soughegan Valley, including Amherst, Brookline, Francestown, Greenfield, Hancock, Hollis, Lyndeborough, Milford, Mount Vernon, New Ipswich, Peterborough and Wilton.
“Alene Candles has been a generous partner of ours for more than 20 years,” said Mike Goodwin, executive director of the Boys & GirlsClub of Souhegan Valley. “This donation will help us introduce even more kids of all ages to science, technology, engineering, arts and math. Our project sand activities will spark curiosity in our younger students and help our teenage students discover the fields that interest them the most, maybe even leading them to a career path.”
For more information about AleneCandles, visit www.alene.com .
For more information about the Boys & Girls Club of Souhegan Valley, visit https://svbgc.org
Alene Candles Celebrates Ten Years of Growth 26 Feb 2019, 12:00 am
February 25, 2019 (Business NH Magazine) - With output growing seven-fold and its workforce quadrupling, Milford-based Alene Candles is celebrating 10 years of growth under the leadership of owners Rod Harl, president, and Ted Goldberg, VP of business development.
According to a statement, friends and colleagues gathered on February 15, to celebrate a successful 10 years at Alene Candles, a leading contract candle manufacturer in the United States, which has expanded its NH-based workforce 150 percent since 2008.
“We are pleased with our sales success, and we are grateful for the contributions from all of our employees. From the moment we started at Alene Candles, our goal has always been to develop and foster a culture where team members enjoy coming to work,” says Harl “We’ve made our employees a priority over the past 10 years by building our employee incentives, increasing wages, and cultivating community programs. Our employees are the key to our success. The labor market has been challenging in recent years, and we are thankful our employees have chosen to join our team. We truly could not make the best candles in the world without them.”
Bringing fresh eyes to the company, Harl and Goldberg sought to build on Alene’s original success, instituting new policies that allowed the company to flourish. Well-known, national brands continued to trust Alene to create their candles. To keep up with demand, Alene Candles built a second facility in New Albany, OH, in 2012 which employs 180 people year-round and grows to 600 during the busy fall months. Simultaneously, the Milford facility expanded its production capabilities, now employing 200 year-round employees; the workforce grows to almost 500 people during peak production.
Above: Milford-based Alene Candles is celebrating 10 years of growth under the leadership of owners Rod Harl, President, and Ted Goldberg, Vice President of Business Development, who are pictured above at the company’s celebration on February 15, 2019.
Alene employees enjoy the festivities at the company’s celebration on February 15, 2019.
Lighting the way 16 Feb 2019, 12:00 am
Milford manufacturer going strong
February 15, 2019 (Nashua Telegraph) - After taking over Alene Candles 10 years ago, business partners Rod Harl and Ted Goldberg are now producing almost seven times the number of candles the company made when ownership changed hands at the end of 2008.
The company, which emits a sweet-smelling fragrance from its factory, marked 10 years of ownership Dec. 30. Officials hosted a company party Friday night to celebrate the strides made in the last decade.
When they first took over, Alene Candles employed 75 people. There are now about 400 year-round workers between two locations. Harl is the president of the company, and said the strides he and Goldberg, vice president, have been able to make through the years is quite remarkable.
“We didn’t set out to do that,” Harl said. “We set out to find a business that worked for both of us.”
After a bit of planning and scoping out possible businesses to purchase, they chose Alene Candles.
Aside from boosting candle production and the number of employees, Harl said Alene Candles is also the first company in New Hampshire to implement a Conscious Leadership model, which embraces 15 commitments. This initiative was unveiled at their New Hampshire location in just the last couple years, while training is continuing at their Ohio location. After purchasing the company from its original owner, Paul Amato, the two businessmen strived to provide their employees with an environment in which they enjoyed coming to work, no matter what his or her role is in the company. That’s where the Conscious Leadership model comes into play.
“We started actually in 2016, testing out these concepts internally, and we started with our executive group, and it’s based on a book called ‘The 15 Commitments of Conscious Leadership’ (The 15 Commitments of Conscious Leadership: A New Paradigm for Sustainable Success),” Harl said. “One of the authors of that book, Diana Chapman, I’ve known since 2014.”
Chapman penned that book with two co-authors, Jim Dethmer and Kaley Warner Klemp. Harl said the first of the 15 commitments they exposed people to uses the phrase “radical responsibility,” which relates to taking 100 percent responsibility in the workplace. Another commitment is “candor,” which relates to having upfront communication in the workplace to avoid having any gossiping occur.
“We brought that internally, actually, at a time in 2016 where we had really some significant cultural challenges here in New Hampshire,” Harl said. “We had some leadership that was not reflecting our company values. As we made changes and started to recover from that, I knew we needed some tough medicine, and Diana’s concepts in this book had really the greatest overlap with the philosophies I wanted to see us embrace as a business.”
The model began with the executive team in 2016, and was then rolled out in New Hampshire in 2017 at all levels of the business. In 2018, this model made its way out to the Ohio location. Harl believes this model will work for other manufacturers as well, and that the 15 concepts can translate into an employee’s daily life, at home with family, or out and about with friends.
Nevertheless, with a second facility, more candles are produced, and are then sent on their way across the U.S. to be purchased. While their candles are primarily sold in the U.S., Harl said some candles also make their way to places such as Europe and the Middle East.
In 2012, they opened their second facility in New Albany, Ohio, which is a suburb of Columbus, Ohio. Harl said this has been a good move for the company, as it serves as a complement to the New Hampshire facility.
“So, we generally start with the more challenging projects in New Hampshire. We have a larger experience base, we’ll deal with the complexity here,” Harl said. “Really, the center of our research and development effort is in New Hampshire.”
He said the newer Ohio facility is a bit smaller, but has a higher output. However, candles are a popular holiday item, and in order to keep up with that seasonal output, the company has to hire temporary workers to meet demands. When it comes time to prepare for the holiday season, the company has to hire hundreds of seasonal workers to meet demands.
“We have about 200 year-round employees here, about 180 year-round employees in Ohio. And we grow to, let’s call it, 1,100 employees in our busiest time of year, which is September, October and November,” Harl said.
He said sometimes the same temporary workers return year after year, with a specific draw from various immigrant population in communities.
However, Harl said while some manufacturing companies across the country encounter a bit of a challenge attracting and retaining qualified workers, Alene Candles does its best to be an attractive employer that provides a good place to work. He said the facility in Ohio is fortunate because it’s part of a manufacturing park. He said New Hampshire is a bit more challenging because there are fewer workers available. Still, they are able to make things work.
How to Adapt Lean Manufacturing for Seasonal Production Demands 19 Dec 2018, 8:48 pm
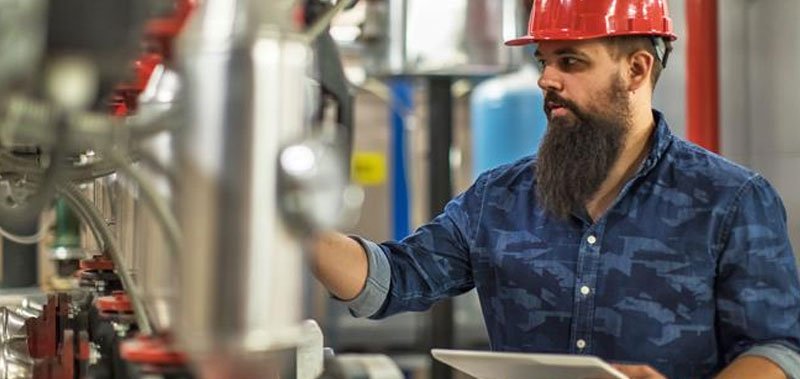
Alene's Journey
Lean Tools
Staffing Concerns
Flexibility Is Key
Q&A with Alene Candles CEO Rod Harl 5 Jul 2018, 12:00 am
July 4, 2018 (New Hampshire Business Review) - Rod Harl is CEO of Alene Candles — a company in the news recently with its annual call for seasonal employees to work on ramped-up production for the Christmas season, which accounts for nearly 40 percent of the growing firm’s sales. He and a partner acquired the Milford company in 2008 from Paul and Nancy Alene Amato, who founded the firm in 1995. The firm does contract manufacturing of candle products for retailers and others, including the beauty supply chain Bath & Body Works.
Q. You have a technical and software background, so how did you become CEO of a candle company in New Hampshire?
A. My business partner and I did start working in the software business, but we parted ways in 2000. In 2006, we reconnected and decided we wanted to work together again. So we spent an entire year looking for companies — I was in Colorado and he was in New York City. We encountered Alene on Memorial Day in 2008 and closed on the company in December. We were very fortunate to find Alene.
The company was smaller, and since then we’ve increased by about sixfold the number of products we make each year, and we’ve grown from 75 to almost 400 employees year-round. Part of that growth has been the buildout of the tech side. We now have a dozen scientists -- techniques used on the technical side aren’t commonly used our industry.
Q. You have a technical and software background, so how did you become CEO of a candle company in New Hampshire?
A. My business partner and I did start working in the software business, but we parted ways in 2000. In 2006, we reconnected and decided we wanted to work together again. So we spent an entire year looking for companies — I was in Colorado and he was in New York City. We encountered Alene on Memorial Day in 2008 and closed on the company in December. We were very fortunate to find Alene.
The company was smaller, and since then we’ve increased by about sixfold the number of products we make each year, and we’ve grown from 75 to almost 400 employees year-round. Part of that growth has been the buildout of the tech side. We now have a dozen scientists -- techniques used on the technical side aren’t commonly used our industry.
Q. You have become something of an evangelist about Conscious Leadership. What is it?
A. It’s a basket of tools that are based on a handful of mindfulness principles. It’s the idea of taking exactly 100 percent responsibility, not more not less, for your role in your work, your home, your life. People get into drama situations when they take on more than 100 percent rather than asking others to accept their own responsibility. But it’s also about giving appreciation and accepting it too. That has more impact on employee satisfaction than spot awards and things like that.
Speaking candidly, I was raised where you don’t confront people with difficult issues – you dance around them. What we teach people is it’s OK to be candid, but lead with your heart. The point is always taken well and the impact for us is that the air of conflict or tension or likelihood that people are going to react poorly – that whole temperature just drops. No one’s forcing a bad interpretation or reaction from them. The way you react is completely under my control or ownership.
We’re teaching people throughout the organization to see it that way, and they’re much more thoughtful in their conversations and how they interact.
Q. And you do mean “the whole organization.”
A. As a mainstream manufacturer, we employ a bunch of people who clock in and out, and what we’ve found is that these conscious leadership tools and principles resonate even more in our case than if we were employing all professionals making healthy salaries.
Q. What was the rollout like?
A. We started this in 2016 at the leadership team level – at the time, there were 12 to 15 of us. I wanted to do a trial balloon to see if I could get buy-in across the top.
Then I met with one of founders of the Conscious Leadership Group, which is based in California. I asked, “What have you done at the hourly level, the factory situation?” They had worked with manufacturing companies before, but they hadn’t gone below the salary ranks. We said, “Let’s give it a shot.” At first, expectations were pretty low. We tried a mix of volunteering and prodding to get people to take part.
But the hourly folks, while they may have been skeptical initially, once you punch through that initial barrier, they were extremely receptive and embraced the ideas because they had never been jaded by the management tool of the month or the job they had in 2002 and they brought in outside consulting trying to espouse teamwork — they were talking to people who were really trying to educate them about using it.
Q. What has the result been?
A. I’m very passionate about this, because these folks have very complicated lives to degrees that we don’t understand or don’t experience often. What we’re able to do is give them some skills to help them manage their own lives that cause shifts that are mind-blowing.
For example, for someone who has a tremendous amount of drama and complexity in their lives this helps reduce the drama, and they’re happier. This is a way to help them enrich their lives.
Emotionally healthy people are more productive employees, turnover goes down and feels good to a manager to hear these stories.
Milford candle company embraces conscious leadership 16 Jun 2018, 12:00 am
June 16, 2018 (New Hampshire Union Leader) - A local candle manufacturer is embracing a philosophy designed to help its employees improve relationships and reduce conflict.
Alene Candles of Milford has enhanced its workforce culture after implementing a conscious leadership program — one of the first companies in the Granite State to adopt the ideology.
The candle company has been working with The Conscious Leadership Group to train its employees on conflict resolution, how to take responsibility for actions, speaking candidly and more.
Rod Harl, president of Alene Candles, recently teamed up with Diana Chapman, a founding partner with The Conscious Leadership Group, to help improve company culture and leadership.
Alene Candles is the first manufacturer to attempt the philosophy on the production floor.
“There was no roadmap for us when this started,” said Harl.
However, Harl said the mindfulness principles have since made employees aware of their emotional states. Harl said they now notice triggers that could anger them or make them anxious and are provided with the tools to relax, de-stress and have a clear mind to make positive choices.
He said some workers were skeptical about the conscious leadership efforts, but but that he continues to hear enthusiasm about the program — not only on the production floor, but also in the home.
“Now that we are doing it, we believe this is a competitive advantage to attracting staff,” he added.
Harl stressed the importance of creating a workforce environment where employees are engaged, valued and appreciated. Management added more supervisors to help solve problems, and the company is focusing on the 15 commitments to improve company culture that is a part of the conscious leadership program, including responsibility, integrity and appreciation.
“We are still early in our journey. We have a lot of work still to do,” Harl said.
Since implementing the program, Harl said workers have less stress, are leaving their shifts less tired and can make more thorough and conscious choices. Worker interactions are more relaxed and pleasant, according to Harl, who said he is pleased with the progress. Alene Candles is one of the state’s largest seasonal employers. Year-round it employs 200 workers at its New Hampshire location, but will reach about 500 employees during its peak holiday season.
Alene Candles is a contract and private-label manufacturer of candles for the gift, cosmetic and retail markets. The company fills tens of thousands of custom-designed, fragranced candles for cosmetic brands and retailers, according to a release.
Milford candle company is hiring 400 seasonal employees 30 May 2018, 12:00 am
May 29, 2018 (Manchester Ink Link) - Alene Candles , the industry leader in full-service contract candle manufacturing, is looking to triple its capacity and production by hiring 400 employees to prepare for the 2018 holiday season. The peak production period ramps up during the summer, as the company prepares for an increase in orders. Alene Candles produces two-thirds of its annual volume between July and December, producing more than 40 million candles during that time frame last year between its two facilities in New Hampshire and Ohio.
“Over the past 10 years, Alene has emerged as one of North America’s largest contract candle manufacturers, fulfilling tens of thousands of custom-designed, fragranced candles for highly-regarded brands and renowned retailers,” said Rod Harl, President, Alene Candles. “We can attribute much of this success to our dedicated workforce which grows in size each summer and fall to help us reach our goal of making best-in-class candles that are gifted to friends and loved ones over the holidays.”
Alene Candles is looking for committed and hardworking people to join the team for seasonal and fulltime employment, as there are numerous opportunities for upward movement within the company. Employees will participate in team building activities, company raffles and giveaways and catered lunches. Alene Candles also embraces the Conscious Leadership philosophy, focusing on building trust and creating a conscious culture, the first company in New Hampshire to do so.
The company is hiring 400 candlemakers over the next two months for both first and second shifts. And while these positions are through mid-December, Alene Candles looks to bring seasonal employees on fulltime whenever possible. Candidates should have a high school diploma or general education degree, a general understanding of operating machinery, good communications skills and manufacturing experience is a plus. The starting hourly rate for candlemakers is $11.25.
In addition to seasonal employment, Alene Candles is looking to fill more than 20 fulltime, year-round positions. These core roles are the backbone of the company, serving in vital positions throughout the candle making process. The hourly rates for these roles vary, starting at $11.25 to $20, depending on the specific position and experience of each candidate. These roles include: pour end and pack out coordinators, line leaders, zone owners, machine operators, wax mixers, materials handlers, quality assurance inspectors and quality assurance team leaders.
Those interested in learning more about Alene Candles and its open positions can call 603-673-5050 ext. 7210 or email hr@alene.com .
About Alene Candles
Alene Candles is a full-service contract and private-label manufacturer of superior custom-designed filled candles for the gift, cosmetic and retail markets. Its industry expertise has allowed it to produce for some of the world’s best-known brands. The company prides itself in exceeding quality and delivery expectations, and in its ability to customize solutions across a range of candle and home-fragrance products. Learn more at
www.alene.com
.
NH employers raise salaries in effort to gain new hires 2 Apr 2018, 12:00 am
April 1, 2018 (New Hampshire Union Leader) - Many employers are boosting wages in a war for new hires.
“You have to stay competitive because everyone is looking” for new hires, said Amy Mayo, a human resources generalist at Associated Grocers of New England in Pembroke.
AGNE, which serves independent grocery stores, is offering $20 an hour for a summer job to fill orders in its warehouse.
“You do have to move quickly (in hiring) if you want a good candidate,” Mayo said at a job fair last week.
New Hampshire in February tied for the nation’s second-lowest unemployment rate, at 2.6 percent, bested by only Hawaii’s 2.1 percent.
The job fair at the University of New Hampshire at Manchester drew 250 job seekers. About 70 employers offered more than 800 jobs collectively.
Some employers “might make an offer or do a job interview right here,” said George Copadis, commissioner of New Hampshire Employment Security, which organized the event.
Yvonne Manning, 55, of Northfield, was looking for an administrative assistant position.
Manning said she sent 100 to 150 resumes and had “not gotten back one callback.”
At the job fair, she said she lined up at least one job interview.
She put her odds of snagging a job as “very good.”
“I got quite a bit of face-to-face,” Manning said. “Some seemed really interested when I told them about my background.”
Copadis said many employers are looking for “someone who’s got a good work ethic” and “someone who’s going to stay with it.”
For job seekers, it’s often about pay, stability and putting them in a position for job growth, he said.
Service Credit Union was looking to hire about 50 people, including tellers, around the state.
“Filling positions is pretty tough, even for our full-time spots,” said employment specialist Anna Roberts.
Teller salaries were raised by a dollar an hour last year, and the credit union “recently did a salary survey,” she said.
At Age at Home, a geriatric care and senior home care management service in Concord, “we could hire at least 10 employees,” said President Laurel Trahan.
Finding qualified people is “incredibly difficult, just with the unemployment rate being so low,” she said. “Younger folks are moving out of state.”
Starting wages range from $11 to $13.50 an hour. Pay rose 50 cents an hour in early 2017 and again at the end of the year, she said.
“I think we’re streamlined to move along the application process quicker,” Trahan said.
Alene Candles in Milford had 30 open positions available.
“We definitely look at other companies on what they’re offering and adjust accordingly,” said HR Manager Jamie Chisholm.
The company raised wages $1 to $2 an hour within the past two years.
Jennifer Donovan at Donovan Equipment Co. in Londonderry said the company has raised wages in some areas and is trying to get an apprentice program started.
Donovan said it’s very difficult to find people as there is a “skills gap” in the workforce.
The company wants to fill seven positions starting at between $14 and $20 an hour.
Cumberland Farms was looking to fill 70 mainly retail openings around the state.
“Some places in New Hampshire can be definitely difficult markets, particularly Manchester and Concord,” said Lindsey White, supervisor of talent acquisition.
Flora Dubois, a talent acquisition specialist, said, “We like to move along right away ... because we could lose our person.”
Samantha Searles, 19, of Merrimack, a freshman at UNH-Manchester, spotted an open position as a “brand ambassador” for Perfect Dental, which called for setting up community events, something she has done with her volunteering elsewhere.
“I found one I really liked,” Searles said.
The 2017 National Candle Association Conference Announces New Changes 7 Jun 2017, 12:00 am
June 6, 2017 (Giftsanddec.com) - Consumer candle safety and fair trade policies are top priorities for the National Candle Association (NCA), which hosted its 2017 Conference & Expo recently in St. Petersburg, FL. Nearly 400 industry professionals gathered for the association’s 43rd annual meeting and exposition.
Among the orders of business at the meeting was the election of the following directors and officers for the 2017-2018 fiscal year: Kathy LaVanier of Renegade Candles was elected NCA President, Bob Nelson of Yankee Candle will continue to serve as Vice President/President Elect, George Pappas II of Lumi-Lite Candle Company will resume his position as 1st Vice President, Tom Donnelly of Alene Candles will serve as 2nd Vice President, and Chris Rakyta of Candle-Lite Company will assume the role of Treasurer.
NCA also seized the occasion of the annual assembly to pay tribute to those whose work has made a significant contribution to the industry or community. NCA’s Hall of Fame Award was bestowed upon two deserving industry leaders in recognition of the lasting impact of their professional dedication: Jeb Head, president of Atkins & Pierce, a seventh generation family-owned company which has served as a supplier to candle makers for 200 years; and John Witham, head of research and development at Candle-Lite, an American candle company founded in 1840.
NCA also recognized ScentsAbility, a nonprofit organization that helps individuals with special needs learn job skills and become independent through making and selling candles.
“Those of us in the US candle sector take great pride in our work and in advancing industry innovation while embracing the heritage of candle making in America,” said Kathy LaVanier, NCA president. “We’re delighted to recognize the achievements of Jeb Head and John Witham, two noted industry leaders, and we applaud the work of ScentsAbility for using candles to help individuals develop life-long skills.”
In addition to the leadership elections and awards, the NCA conference agenda included trend sessions, research presentations, board and committee meetings, and the annual business meeting. Association priorities for the coming year include its ongoing commitment to candle safety and consumer education about safe candle use, and sustaining fair trade policies to maintain a balanced and competitive market in the US for American candle companies.
Milford business runs made-to-order operation 21 Apr 2013, 12:00 am
April 20, 2013 (Nashua Telegraph) - Alene Candles manufactures millions of products ever year, but employees say their practice is more of an art form than anything else.
Kellie Church, of Wilton, has worked at the company for 15 years in the production lab. She is so highly skilled at perfecting and modifying specialty candles that today, she can eyeball the precise mixtures required to create the subtle differences between the orange colors “peach” and “apricot nectar.”
Lab Manager Peggy LaFrance said at the small laboratory across the street from the manufacturing location on Scarborough Lane each one of Alene’s middle to high end candles are meticulously created, formulated and tested for weeks on end.
“It’s a craft,” she said.
Selling to stores like Neiman Marcus, The Limited and Bath & Body Works, LaFrance calls on about 10 lab technicians, a chemist and a chemical engineer to perfect millions of candles that will go into production every year. Alene Candles has also designed novelty candle items in the past for the White Castle restaurant and singer Gwen Stefani’s designer brand L.A.M.B.
Alene Candles formed in 1995, first in Wilton, before moving to Milford under the direction of founder Paul Amato. The company is a private-label filler. So, while they compete with candle manufacturers like Yankee Candle in Massachusetts, they offer “turnkey and non-turnkey services,” too. That means they’ll design products for their customers, from packaging to fragrance, or just fill an order for a special customer by making the wax candle.
At the Alene lab, it can take anywhere from four to six weeks for a candle to be fully tested. Technicians work to melt the wax, getting the proportions of paraffin, soy and soft wax just right, before experimenting with color and smell. A few test samples of the candles are made and placed under incandescent and fluorescent lighting for weeks to ensure the mixtures won’t fade over time. Then the candles are tested in the specialty “burn lab” to test for “wick optimization” and other safety properties.
In a long, dark room, Manager Andrew Masse stood looking out over dozens and dozens of lit candles, set to burn in four or eight hour shifts this past week. He is tasked with monitoring the candles’ burning and to ensure there is no “flash over,” the disastrous moment when a candle is so poorly mixed together, the wax and container light on fire. Masse said that rarely happens at Alene but somebody always has to stand by to keep a careful watch and be sure the product is completely safe.
He joked he tells his wife Amanda that she can only burn the specialty candles he’s approved.
Over at the manufacturing plant, where more than 150 people work, lines of employees put out thousands of candles every day.
In a typical 8-hour shift, Jack Kuehl, Alene’s manager of manufacturing, said workers can turn out anywhere from 8,000 to 40,000 candles at their 75,000-square-foot location, depending on the order.
Amato, who founded the company with his wife Nancy Alene Amato, sold the company in 2008 and is now a minority shareholder.
He said Alene is not at danger for competing with overseas manufacturing at China and other places because of “quality.”
He added few people take the time to develop such candles so carefully but that is part of Alene’s signature process. And while dozens of perfumes and candle scents blend together to omit an overwhelming smell at the Alene site, workers say they have grown so accustomed to it.
Mayeen Nguyen, of Nashua, stood looking out over a few workers using towels to wipe away melted candle wax on glass containers before the hundreds of fragrant candles before they went out for shipment. She said she enjoys her job.
“And I don’t even smell it,” she said with a smile.
The company also recently received more than $60,000 as a job training fund grant from the state to improve their practices.
Chuck Tewell, Alene Candles vice president of human resources, said the training of their employees, to improve their workers’ skills as well as company practices, is set to go into effect later this year.
Samantha Allen can be reached at 594-6426 or sallen@nashuatelegraph.com. Also, follow Allen on Twitter (@Telegraph_SamA).
Alene Candles Joins Ohio Beauty Campus 18 Jul 2012, 12:00 am
Multi-million-dollar facility creates jobs at supply chain hub
July 18, 2012 (Beauty Packaging)
- Ohio's tax incentives, combined with the advantageous supply chain generated by multiple associated vendors in close proximity, has spurred the growth of a personal care and beauty campus near Columbus, OH.
The latest to join the movement is Alene Candles, which has opened a new multi-million-dollar facility that it says will create approximately 135 permanent new jobs and 350 seasonal jobs at its New Albany campus.
Alene Candles is a full-service contract manufacturer of superior-quality, custom-designed candles and home fragrance products for the gift, cosmetic, and retail markets.
President Rod Harl of the Milford, NH-based private-label company made the announcement at the 300,000-square-foot facility in New Albany's booming Personal Care and Beauty Innovation Campus, which is located on the outskirts of Columbus.
Alene Candles leases approximately one-third of the facility.
Harl said the location provides Alene Candles with facilities for manufacturing, distribution, and research and development. "The advantages of this location are not only access to the Midwest market, but its strategic location for U.S. distribution."
The Personal Care and Beauty Innovation Campus is part of a regional effort to spur growth and inspire innovation among similar business sectors by dividing sections of the New Albany business park into discrete "innovation campuses." In addition to Alene Candles, the Knowlton Development Corp., VeePak, Axium Plastics, and Accel Inc. are among several leading national and international personal care companies that have moved into what has become one of the fastest-growing supply chain hubs in the Midwest.
Harl explained that this highly integrated supply chain hub is designed to support companies within the beauty and personal care sectors that can mutually benefit from complementary capabilities, interrelated supply chains, and creative synergies.
He noted that Alene Candles works with Limited Brands, Estée Lauder, Crabtree & Evelyn, Coty, Williams-Sonoma Inc., L'Oréal, among other national and international beauty and personal care products brands.
Alene Candles had been exploring expansion sites in other states, but tax credits of more than $300,000 from the Ohio Tax Credit Authority were key, Harl said. Local tax incentives from the City of New Albany also were offered to companies in the campus.
"Other states made a big push for the Alene expansion jobs, but Ohio's offer was very competitive," Harl said. "Combined with the central location and the proximity to other companies with which we do business, it was an offer we couldn't refuse."
Harl noted that the fact that the beauty innovation campus is LEED (Leadership in Energy and Environmental Design) Silver Certified was significant as well. "We're employing any number of best practices that will measurably reduce our plant's energy footprint, so we're very pleased to achieve that goal," he said, adding that all facilities within the beauty innovation campus meet LEED standards.
While the facility incorporates some state-of-the-art automation, it is not a highly automated facility in the context of U.S. manufacturing, Harl explained. "Achieving the quality our customers expect still requires a degree of human touch. As a private label producer, this facility gives us the right mix of quality, efficiency, and cost savings."
Alene Candle: Turning Up The Heat with Lean 1 Jun 2011, 12:00 am
Alene Candle is a contract candle manufacturer in NH. A team of 130 develops, designs, produces & tests more than 17 million candles annually. Alene set out to "do lean" to achieve greater levels of productivity and have done that and so much more!
June 1, 2011 (Newswire.com) - Alene Candle LLC, located in Milford, New Hampshire is a full-service contract candle manufacturer. In business since 1995, the company now manufacturers more than 17 million candles annually, bringing an artisan's touch to private label candle brands for the gift, cosmetic, and retail markets. Alene's team of over 130 people develops, designs, produces and tests its candles to exacting specifications.
In order to continue this trend, Alene Candle's President, Rodney Harl, asked GBMP to help the company determine how to achieve greater levels of productivity and improve key operational metrics. As a highly seasonal business, Mr. Harl was especially interested in introducing simple, standardized methods so that the company could reduce waste and more easily re-balance staffing when volume increases dramatically to support the high season.
Enter GBMP Continuous Improvement Manager/Master Black Belt, Ron Pujalte. Through a customized program of training and targeted Kaizen Events, Ron has helped Alene tap into the knowledge and creativity of Alene employees and the results are really starting to show.
For example, as part of a Value Stream Mapping event in January, the team completed a spaghetti diagram for part of the production process, and then put in place a new process that cut walking from 8.35 miles per operator per shift to .45 miles per operator per shift!
In a February 2011 Kaizen event focused on small-component management, a cross functional team focused on simple work place organization in specific inventory and on-floor storage, and also put kanbans in place for some of the commonly used materials at the end of the production line. They also made improvements to the information flow, saving 162 miles of walking per year!
In March Alene focused on their packing process, collecting cycle times on all the process steps, analyzing the data, then developing and testing new standards for each line position. The team then created visual work and cleaning instructions for all positions and established a standard card to use in documenting the instructions. This method is especially helpful at Alene, a plant where many different languages are spoken by employees and where use of temporary labor is critical in the high season. The Kaizen Team also set up visual communication devices (andons) so line employees can easily signal the Line Leader or QA, Maintenance or Group Leaders when there is a problem.
In April a team worked on a finished goods inventory management process and identified ways to eliminate 84 weeks of non - valued activities through the use of mistake proofing techniques (Poka-Yoke).
In the most recent Kaizen event, an Alene team attacked three warehouses and established better linkage between the pack out process and the warehouses. Over 5 days the team freed up over 120 pallet locations and implemented a pull system (which resulted in hundreds of miles saved in transit) between warehouse operations and the pack out process.
Ron is confident the changes made so far will continue to grow and have a positive impact, especially during the heavy summer/fall production period. "The people at Alene have great ideas and are moving pretty quickly to get them implemented. They are getting good support from the Lean Steering Team we established, and I am continuing to challenge them to complete improvement projects before the busy season comes."
Alene President Rodney Harl is also very pleased with the efforts his team has made and is looking forward to seeing what else his creative employees can do. "I have made it a point to walk around to see and talk with folks about the improvements they have made, and they are so effective, yet often elegantly simple. Small changes for the better every week are what we are getting and Ron has been great at helping us learn how to engage people and target key areas that can make or break us when we are really busy. When you are undergoing growth, you have to be mindful of NOT growing your costs in line with your revenue, and continuous improvement is helping all Alene employees see how to do this."
Candle company adding location 31 Mar 2011, 12:00 am
Candle company adding Ohio location
March 31, 2011 (Nashua Telegraph) - Alene Candles, the fragrance candle company, is expanding into Ohio. The firm is keeping its Milford plant, Vice President Ted Goldberg said.
According to Columbus Business First, an Ohio business journal, Alene received job tax credits from the state of Ohio worth an estimated $214,000 over seven years, and Alene promised an $8.2 million project expected to create 135 jobs.
Goldberg said Alene has grown significantly over the past several years and needs to expand.
It ships candles all over the country, he said, and the new location in New Albany, Ohio, will make that easier.